Although purchasing more and better capital leads to higher productivity, explanations for when and why firms choose to adopt new technology are not straightforward. In this article, we shed some light on how manufacturers choose to adopt new technology by purchasing equipment. The decision can be complicated, so we surveyed manufacturers to get insights into how they approach it. We find that the top two reasons manufacturers invest in new equipment with advanced technology is to keep up with competitors and save on labor costs. But upgrading is not always an obvious choice. Manufacturers cite credit constraints and uncertainty about how beneficial the new technology will be as key barriers to making new investments.
The decision to purchase new equipment is complicated
In standard economic theory, manufacturers purchase equipment for their factories when the expected benefits of the purchase are greater than the expected costs. In practice, assessing expected benefits and costs is complicated. There may be uncertainty about the potential benefits of the new technology, and the costs include not just the price of the equipment, but also the resources spent in searching for the right product, getting a loan to pay for it, stopping production to install it, and learning how to use it. The companion paper to this CFI article finds evidence that equipment purchasing decisions are indeed complicated ones for manufacturers. That paper uses administrative U.S. Census Bureau data to examine what happens after manufacturing plants experience flooding—particularly from floods that are declared major disasters by the U.S. President. Some plants, especially those that were low performers before the disaster happened, close; however, the ones that stay open typically upgrade their damaged equipment and experience a boost in labor productivity. The companion paper also finds that as the lower-productivity plants shut down, excess secondhand machinery is purchased by higher-productivity plants, including young plants and the plants of new entrants (i.e., their newly built plants or the used ones they bought). On net, machines are redistributed toward better use, and labor productivity in the manufacturing sector typically goes up in places that experience a flood.1
So, what are we to make of the finding that manufacturing productivity rises after floods? One interpretation is that manufacturers that don’t experience floods are leaving money on the table by not investing in readily available productivity-enhancing equipment. But it’s more likely that floods lead manufacturers to rethink their production equipment investments as they rebuild their operations and that expanded access to financing due to federal disaster relief helps them pay for new equipment. The federal government provides low-interest recovery loans to firms’ flood-damaged plants and, as shown in another paper, also indirectly boosts smaller and younger firms’ access to bank credit. Expanded access to credit can explain why smaller manufacturers, which are typically more sensitive to credit barriers, invest more in equipment and see higher productivity gains than larger firms after flooding.
The research that we’ve just summarized suggests the decision by manufacturers to purchase equipment is complicated. So, what do they actually think about when considering whether or not to purchase new equipment? In a recent survey, we asked manufacturers directly about their decision-making process. The survey was disseminated to manufacturing firms affiliated with the Chicago Fed Survey of Economic Conditions (CFSEC), as well as manufacturers affiliated with the Wisconsin Center for Manufacturing and Productivity (WCMP), the National Institute of Standards and Technology’s Manufacturing Extension Partnership (NIST MEP), and the Center for Industrial Research and Service (CIRAS) at Iowa State University. In total, we received 20 responses from CEOs and other high-level executives at manufacturing firms. While not a large number of responses, 20 is enough for a few key themes to emerge that help us better understand what matters most for manufacturers’ investment decisions—and how plants may behave when a natural disaster forces plant managers to rethink their production process and technology mix.
Manufacturers invest to keep up with competitors and save on labor
The fundamental reason manufacturers purchase new equipment is to increase profits, but what exactly drives the why and when of manufacturers’ investment decisions? According to our survey respondents, the number one reason for investing in new technology is to stay competitive—about 85% picked this answer (see figure 1). More so than firms in many other industries, manufacturers often sell in large national or international markets. In general, the larger the market, the more competitive it is. So, our finding that maintaining competitiveness is top of mind for manufacturers makes sense.
1. Why do manufacturers invest in new technology?
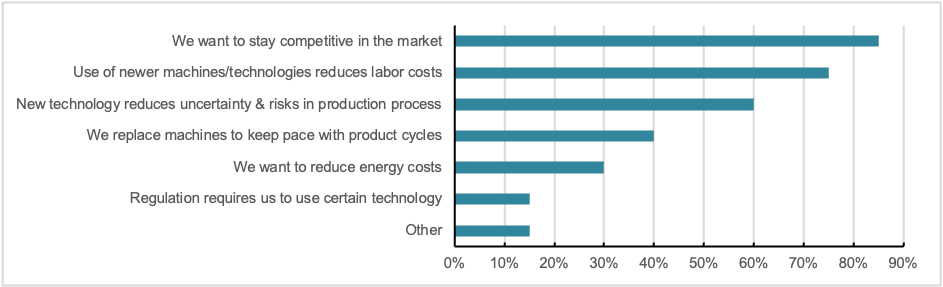
The number two reason survey respondents gave for investing in new technology is that new equipment helps them save on labor costs. Another way of expressing this is that machines help workers be more productive. Machines can automate certain tasks, freeing up workers to do other useful things and reducing the labor cost per item produced. Figure 1 shows that there are other factors at play in the decision to invest in new technology: Updated equipment can improve the production process or reduce energy costs. In addition, some manufacturers buy equipment in alignment with a product cycle or to meet regulatory requirements.
Financing constraints and uncertainty about the benefits of new technology are the top reasons manufacturers hold back on new equipment purchases
As we discussed earlier, the cost of purchasing new equipment is not just what’s on the price tag. Manufacturing equipment is often very expensive and complex, requiring financing, reconfiguration of buildings for installation, retraining of workers, and figuring out how to integrate the equipment into the production process. Of all these costs, access to financing is the most important among the survey respondents, which is captured by three of the categories shown in figure 2: lack of personal finances, could not get private loan, and could not get government loan/grant. Respondents highlighted limited cash flow and high interest rates as key barriers to such access. Some respondents also noted that financing constraints may lead them to buy cheaper secondhand machines, potentially forgoing more advanced technology available with newer machines.
2. Barriers to investing in new technology
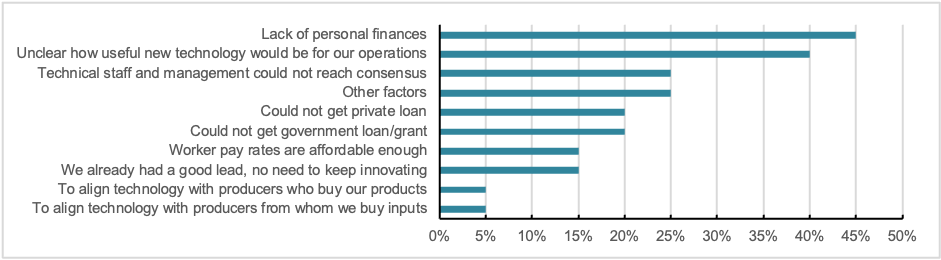
According to the survey respondents, the number two barrier to purchasing productivity-enhancing equipment is uncertainty about whether the new technology would actually be beneficial for their operations. The companion paper suggests that on average, new equipment does raise productivity, but there is no guarantee for any individual firm that a new machine would integrate well with their existing processes and yield productivity gains. Such uncertainty about the usefulness of (or return on) a new equipment purchase is made especially salient by the fact that machinery installation often involves additional costs such as stopping current revenue-generating production.
If manufacturers were forced to purchase new equipment, they would often look to upgrade
Usually, manufacturers considering purchasing equipment have the option to do nothing, but the companion paper highlights a situation when they can’t, and we wanted to better understand how survey respondents would approach it. In the survey, we asked respondents to consider hypothetical scenarios where a flood caused either a 5%, 25%, or 65% loss to the value of their equipment. Would they shut down entirely, relocate, repair and continue operating, or replace and continue operating?
Many survey respondents indicated that in the lower loss scenarios after a flood (with a 5% or 25% loss), they expected to be able to repair and continue operating. In the 5% loss scenario, the vast majority (75% of respondents) indicated they would likely make repairs; and in the 25% loss scenario, 40% of them indicated they would make repairs, while 35% indicated they would probably upgrade. However, if equipment were severely damaged (as in the 65% loss scenario), the largest share of respondents (35%) indicated that they would look to upgrade their equipment (see figure 3). One respondent stated that a destructive disaster would be an “opportunity to modernize,” and another noted that “when replacing by necessity, [we should] stay current.” To pay for the repairs or new equipment, respondents indicated that they would likely rely on insurance payouts and government or private loans that would be accessible after a flood. They also indicated that in the absence of a disaster, they have limited resources to upgrade.
3. What manufacturers would do if they experienced major damage to their equipment
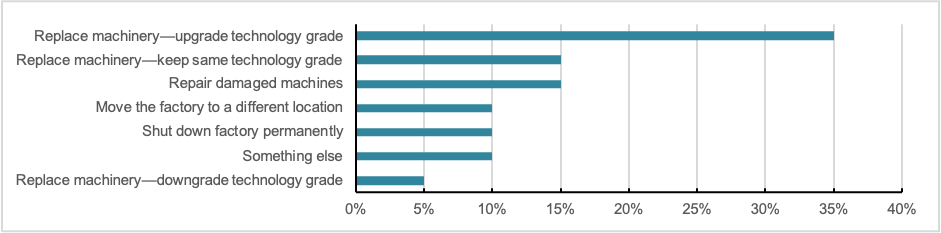
As we noted earlier, one important cost associated with upgrading equipment is using resources to determine whether new technology is a good fit (resources that could be used instead for revenue-generating production). One respondent who indicated they would upgrade if their factory faced a major disaster stated that normally, “I would not have time to investigate new technology.” Thus, there is a potential silver lining from unexpected disasters: By forcing a production shutdown, such events lower the opportunity cost of considering a technology upgrade.
Overall, the survey results suggest that when manufacturers face a major destructive episode like a flood, there is a good chance they will upgrade their equipment if they have access to insurance payouts and financing.
Conclusion
New technology is a key driver of economic growth, but the process of technology adoption is complicated, especially when it involves purchasing expensive complex equipment. In a recent survey, we asked manufacturers how they approach the decision to purchase such equipment. We found that staying competitive and lowering labor costs were the most important drivers for manufacturers to make new equipment investments. But there are important barriers to making these investments beyond just the cost of the equipment. Financing constraints and uncertainty about the usefulness of new equipment are the top reasons for manufacturers not to make such investments, according to the survey results. The survey results also indicate that when manufacturers face a major natural disaster like a flood, there’s a decent chance they will upgrade to higher-productivity equipment if they have access to insurance payments and credit.
The results of our survey are consistent with the companion paper, which finds that after floods, there is substantial machinery replacement among rebuilding plants as well as a redistribution of machinery across plants. The disaster affecting plants forces manufacturers to rethink their production machinery mix, and the accompanying government recovery spending expands firms’ access to financing. Overall, after floods, manufacturing productivity goes up.
Taken together, the survey results and the companion paper raise an interesting question: Are there new policies that could reduce barriers to new equipment investment and boost manufacturing productivity the way that natural disasters do?
Details for Thomas Walstrum are available on his Chicago Fed online profile (accessed by clicking his name in the byline). Tarikua Erda is a PhD candidate in sustainable development at Columbia University.
Notes
1 This does not mean or imply that floods are a good thing on net for a local area—often lives and livelihoods are lost, and recovery is a major stress for the affected communities. But once a disaster has happened, expanded access to financing in the post-disaster rebuilding period can push manufacturers toward achieving higher productivity, which helps facilitate economic renewal in the broader region.