Introduction and summary
Mexico has become one of the world’s leading producers and exporters of motor vehicles, although it has no automakers of its own. During the more than two decades under the North American Free Trade Agreement (NAFTA, entered into by the United States, Canada, and Mexico), Mexico’s light vehicle production more than tripled—from 1.1 million units in 1994 to nearly 3.5 million units in 2016. Moreover, Mexico’s light vehicle exports increased from 579,000 to 2.8 million units during the same period.1 By 2016, motor vehicle assembly and parts plants employed 735,472 workers in Mexico.2 Mexico is the low-wage country among NAFTA partners. Over the period 2007–14, on average, wages in motor vehicle assembly represented around one-fifth of those in the United States and wages in the production of motor vehicle parts about one-eighth.3 According to one 2016 news article on trade trends, after a recent growth spurt, the automotive sector now represents 25 percent of Mexico’s manufacturing exports and over 3 percent of the country’s gross domestic product (GDP).4
In this article, we explore the impact of NAFTA on Mexico’s motor vehicle industry—specifically, on Mexico’s integration into North America’s automotive industry and the subsequent increase in intra-industry trade in automobiles.5 The auto industry has undergone dramatic changes over the past 20-plus years. First, we provide a brief summary of the history of auto production and related trade policies in Mexico before NAFTA. Then we provide a detailed analysis of Mexico’s light vehicle production and exports from 1990 through 2016. Our analysis shows how Mexico has become an integral part of North America’s motor vehicle industry. In addition to aggregated industry-wide statistics, we are able to draw on data that identify the specific country of sale for vehicles produced in Mexico. These data are available on an annual basis from 2005 through 2014. Finally, we discuss how the observed trends in Mexico’s light vehicle production and trade have affected the spatial distribution of auto production within Mexico and across North America. We show that as in the United States, the motor vehicle industry has agglomerated in Mexico.
A brief history of Mexico’s auto production and trade policies before NAFTA
Mexico has a long history of motor vehicle production by international automakers. The first entrant was Ford, which began to assemble Model Ts in Mexico City in 1925.6 General Motors (GM) and Chrysler built their first assembly plants in Mexico during the 1930s (Werner, 1993). By 1960, a dozen companies were assembling vehicles in Mexico and supplying most of the domestic market (Klier and Rubenstein, 2013b; and Moreno Brid, 1992, p. 260).
A key factor in shaping the development of Mexico’s auto industry was the country’s industry-specific trade policies. During the first half of the twentieth century, vehicles sold in Mexico were either imported as finished products or put together at small-scale assembly plants (Klier and Rubenstein, 2013b).
Automotive decrees issued in 1947 and 1962 limited the ability of international automakers to assemble vehicles in Mexico and to use imported parts (Healy, 2016, pp. 39–40; Moreno Brid, 1992, pp. 260–261; and Moreno Brid, 1996). The 1947 decree imposed quotas on the import of parts to assembly plants. In 1962, the Mexican government started implementing a policy of import substitution, favoring domestic production over imports. That policy prohibited imports of finished vehicles, engines, and other auto parts, significantly raising trade barriers for Mexico’s auto industry. As a result, the 1962 decree compelled every carmaker to alter operations in Mexico: It stimulated the construction of several vehicle assembly and engine plants. For instance, Ford built a new assembly plant at Cuautitlán in 1964, and Chrysler at Toluca in 1968.7 Notably, around the same time, Nissan and Volkswagen built their first full-scale assembly plants in Mexico—Volkswagen at Puebla in 1965 and Nissan at Cuernavaca in 1966. All four plants were located in the center of Mexico, within 90 miles of Mexico City. After the 1962 decree, many of the other automakers stopped assembling and selling vehicles in Mexico. The surviving plants saw a noticeable increase in the volume of production, from 48,841 vehicles in total in 1962 to 189,000 in 1970.
Yet the 1962 decree did little to improve the competitiveness of Mexico’s auto industry (Womack, Jones, and Roos, 1991, pp. 264–265). The Mexico-produced vehicles “were of poorer quality and entailed higher production costs than their foreign counterparts” (Moreno Brid, 1996). Subsequently, a series of automotive decrees during the 1970s and 1980s moderately loosened trade barriers while continuing to protect the domestic production of vehicles (Moreno Brid, 1996). In the process, Mexico’s light vehicle production grew rapidly during those two decades, from 189,000 in 1970 to 490,000 in 1980 and 801,000 in 1990. By 1981, when GM opened its Ramos Arizpe plant, the Big Three automakers (Chrysler, Ford, and GM) each had two full-scale assembly plants in Mexico. A few years later, Ford became the first among the Big Three (today referred to as the Detroit Three) to replace its original plant; in 1986 it opened a new plant in Hermosillo, two years after closing its original Mexico City plant.8
By 1983 the Mexican government shifted its auto industry policy again, this time focusing on export promotion. Vehicle producers responded by opening modern and competitive plants (Klier and Rubenstein, 2013b). This represented the start of the process of integrating Mexico into North America’s auto industry.
The automotive decree of 1989 permitted imports to account for 20 percent of each automaker’s sales in Mexico, as long as the value of its exports from Mexico exceeded that of its imports. The 1989 decree also set the local content requirements to 36 percent (Moreno Brid, 1996; and Womack, Jones, and Roos, 1991, p. 266). According to Hufbauer and Schott (2005, p. 369), “the Mexican Automotive Decree of 1989 substantially liberalized Mexican rules on the auto industry, even though the national value added requirement and native ownership requirement remained huge impediments to industry rationalization.”
A significant step toward Mexico’s market integration with the United States was the establishment of the maquiladora (sometimes called maquila) program (Russell, 2016, pp. 389–390). Maquiladoras are manufacturing operations in Mexico that assemble imported components into exportable products; the attraction of this program was twofold—inputs from the United States were imported to Mexico tariff-free (provided the maquiladora output would be exported back), and on the U.S. side, tariffs were incurred on only the value that was added in Mexico (De La Cruz et al., 2011, p. 4). The Border Industrialization Program (BIP) authorizing maquiladora plants had been established by Mexico back in 1965, but the auto industry did not take full advantage of the program until the 1980s (De La Cruz et al., 2011, p. 4). By the late 1980s, BIP had been used quite heavily for plants producing motor vehicle parts. Maquiladoras boomed in the 1980s, when a collapse in the value of the peso beginning in 1982 created irresistibly low costs of doing business in Mexico,9 aside from the easing of trade barriers (Wilson, 2010; and Berry, Grilli, and López-de-Silanes, 1992, pp. 25, 28). The number of automotive maquiladoras increased from 53 in 1980 to 187 in 1990 and 313 in 2006 (Berry, Grilli, and López-de-Silanes, 1992, table 4; and Murphy and McDonough, 2012, p. 427).
Of greater importance for the auto sector was the enactment of PITEX (Programa de Importación Temporal para Producir Artículos de Exportación) in 1990. The maquiladora program was designed primarily for foreign-owned companies that wanted to import nearly all of their inputs and subsequently export their production. PITEX allowed domestic as well as foreign-owned companies to sell most of their production in Mexico (Rice, 1998, p. 380). For example, an auto parts supplier that sold most of its output to an assembly plant in Mexico could qualify for tariff relief under PITEX, but not as a maquiladora. Consequently, as of 2006, auto-related manufacturers accounted for 48.7 percent of exports of all firms registered under the PITEX program, but only 6.2 percent of exports of all maquiladora plants (De La Cruz et al., 2011, pp. 7–8). In November 2006, the maquiladora and PITEX programs were merged into a single program called IMMEX (Industria Manufacturera, Maquiladora y de Servicios de Exportación) (De La Cruz et al., 2011, p. 5).
Mexico’s integration with the North American market
The implementation of NAFTA, which began in 1994, removed most of Mexico’s remaining trade restrictions with its neighbors to the north over a period of ten years. Annex 300-A of NAFTA spells out the details of liberalizing trade in the auto industry. Key provisions affecting Mexico’s auto industry included the following:
- For every $1 worth of imported vehicles, the required minimum value of exports declined from $1.75 in 1993 to $0.80 in 1994, $0.55 in 2003, and zero dollars in 2004.
- The minimum requirement for Mexican content for duty-free export declined from 36 percent in 1993 to 34 percent in 1994, 29 percent in 2003, and zero percent in 2004.
- Import duties declined from 20 percent in 1993 to 10 percent in 1994 and zero percent in 2004.
- Parts plants in Mexico were permitted to be 100 percent owned by foreigners after 1998 (Moreno Brid, 1996; Ramírez de la O, 1998, p. 65; and Studer, 1994, pp. 27–29).
The five “legacy” automakers (Chrysler, Ford, GM, Nissan, and VW), with production facilities in Mexico prior to the implementation of NAFTA, received a head start in the free trade era.10 In addition, for all automakers, in order to qualify for duty-free export from Mexico after 2002, at least 62.5 percent of a vehicle’s content had to be made somewhere in North America (Studer, 1994, pp. 28–29; and Hufbauer and Schott, 2005, p. 369). That threshold was raised from a previous 50 percent requirement to keep foreign automotive producers (in particular Japanese carmakers) from using Mexico as an export platform for selling into the United States (Hufbauer and Schott, 2005, p. 369).
At the time of the NAFTA negotiations, many analysts questioned whether Mexico’s motor vehicle industry would benefit from tighter integration with the United States’. For example, the Office of Technology Assessment (OTA) of the U.S. Congress found “little reason to believe that existing efficient capacity with a high utilization rate in the United States or Canada would be closed and replaced by production in Mexico” (U.S. Congress, Office of Technology Assessment, 1992, p. 133). The OTA also explained that “most of the [foreign] companies have assembly plants near Mexico City that primarily serve the domestic market. Historically, these have been profitable only because of trade barriers; if a North American Free Trade Agreement (NAFTA) sharply lowered those barriers, these plants would have to reduce their costs and improve their productivity to remain viable” (U.S. Congress, Office of Technology Assessment, 1992, p. 133). The OTA concluded that “in the short term, then, neither the Big Three nor transplant assemblers can expect to substantially improve their competitive positions by moving production to Mexico” (U.S. Congress, Office of Technology Assessment, 1992, p. 133).
In reality, NAFTA negotiations stimulated a round of investment by the country’s five legacy carmakers, resulting in vehicle assembly plants in Mexico receiving state-of-the-art technology (Klier and Rubenstein, 2013b). For example, in anticipation of NAFTA, three full-scale assembly plants were opened during the early 1990s (one each by Chrysler, GM, and Nissan). In addition, to meet NAFTA’s requirements that some production be located in Mexico in order to be able to import vehicles, Honda and Toyota for the first time began production in Mexico—at small-scale plants in El Salto (in 1995) and Tijuana (in 2004), respectively.
With the implementation of NAFTA, Mexico opened up its market. As a result, auto manufacturers started to optimize their production operations within the entire economic space of North America. In the process, vehicle assembly facilities in Mexico adopted the latest technology and became essentially interchangeable with those in the United States and Canada. For example, the PT Cruiser, sold by Chrysler over model years 2001–10, was assembled exclusively at the company’s plant in Toluca, Mexico.
For Mexico, NAFTA also proved to be the trigger for negotiating trade agreements with many other countries (Villarreal, 2017). Through its free trade agreements, Mexico gained “tariff-free access to 47 percent of the global new vehicle market in 2015” (Swiecki and Menk, 2016, p. 17). As of 2016, Mexico had reached 14 agreements with 46 countries (Iliff, 2016a). As Villarreal (2017) noted, “Mexico’s pursuit of free trade agreements with other countries is a way to bring benefits to the economy, but also to reduce its economic dependence on the United States.”
Under NAFTA, there was a ten-year transition period for phasing out most of the trade barriers that had existed before. After the conclusion of that period in 2004, a large number of foreign-headquartered carmakers announced plans to assemble vehicles in Mexico for the first time. BMW, Daimler’s Mercedes-Benz, Hyundai Motor Group’s Kia Motors, Mazda, and Volkswagen Group’s Audi subsidiary were all set to begin production between 2013 and 2020, raising the number of vehicle producers to 11. The number of assembly plants in Mexico was set to increase from 11 in 2004 to 21 in 2020.
Only two of the ten additional plants built since 2004 will have been built by the Detroit Three producers. Thus, the Detroit Three producers’ share of Mexico’s light vehicle production is set to continue to decline: For instance, their production share decreased from 56 percent in 2005 to 45 percent in 2016. Moreover, their share of light vehicle sales within Mexico fell from 50 percent to 32 percent over the same period.11 Thus, under NAFTA, Mexico’s auto industry not only became much more integrated with those of the United States and Canada, it also became much more international in nature.
Mexico’s light vehicle production under NAFTA
Light vehicle production in Mexico increased from 821,000 in 1990 to nearly 3.5 million in 2016—an average annual increase of 13 percent (figure 1).12 Most of the increase in Mexico has come in two spurts. First, over the first five years under NAFTA, light vehicle production increased from 930,000 in 1995 to 1.9 million in 2000. Second, after four straight years of decline, Mexico’s light vehicle production increased from around 1.5 million in 2004 to almost 3.5 million in 2016. The Detroit Three’s production share in Mexico has been declining since 2004, when the transition agreements associated with NAFTA implementation had run their course. Mexico had traditionally been the backyard of the Detroit Three’s North American operations (their operations in Mexico primarily served the Mexican market). Between 1985 and 2004, the Detroit Three producers, on average, accounted for 62 percent of Mexico’s light vehicle production. Subsequently, as more overseas-headquartered producers entered Mexico, that share had dropped to an average of 52 percent during 2005–16 (with Detroit Three production coming in below 50 percent in 2015 and 2016).13 To put it differently, Chrysler (now Fiat Chrysler Automobiles, or FCA),14 Ford, and GM together accounted for only 36 percent of the increase in Mexico’s light vehicle production (2.54 million units) between 1995 and 2016.15
Figure 1. Mexico’s light vehicle production and share of North America’s production, 1990–2016
Given the growth in light vehicle production volumes in Mexico, the country’s share of North America’s production increased from 6.2 percent in 1995 to 10.9 percent in 2000, 18.9 percent in 2010, and 19.5 percent in 2016 (figure 1). Between 1995 and 2016, the share of North America’s light vehicle production decreased in the United States from 78 percent to 67 percent and in Canada from 16 percent to 13 percent (table 1).
Table 1. North America’s light vehicle production, by country, 1990–2016

Source: Authors’ calculations based on data from WardsAuto InfoBank.
How much a particular country accounts for the change in North America’s light vehicle production will differ depending on the chosen time frame. Mexico accounted for just over 90 percent of the 2.8 million unit increase in light vehicle production in North America between 1995 and 2016. However, Mexico accounted for only about one-half of the 5.5 million unit increase in the region’s production of light vehicles between 1990 and 2016 and only around one-fifth of the 5.8 million unit increase between 2010 and 2016 (table 2).16
Table 2. Change in North America’s light vehicle production, by country and time period

Source: Authors’ calculations based on data from WardsAuto InfoBank.
Mexico’s share of light vehicle production in North America is likely to increase further in the years ahead. As of year-end 2016, four assembly plants were under construction in North America; three of the four were in Mexico and only one in the United States (by Volvo in South Carolina). According to WardsAuto Forecasts, Mexico will account for just under 26 percent of North America’s automotive production by 2023.17
The importance of Mexico as an auto production location in North America varies by carmaker. Among Mexico’s five leading producers, at the high end VW had 82 percent of its North American production in Mexico in 2016, whereas the Detroit Three producers’ shares ranged from 13 percent to 20 percent (table 3). Nissan, which fell between the extremes, with 45 percent of its North American production in Mexico in 2016, more than doubled the share of its North American production located in Mexico in 1995. By comparison, in 1995, near the start of NAFTA’s implementation, the production share in Mexico was lower for four of the five large auto producers assembling vehicles there back then: Each of the Detroit Three automakers had between 4 percent and 8 percent of their respective North American production in Mexico, and Nissan had 17 percent. VW was the exception: All of its North American production was located in Mexico in 1995; it wasn’t until 2011 that the company opened an assembly plant in Tennessee.
Table 3. Light vehicle production in Mexico, by automaker, 1995 and 2016
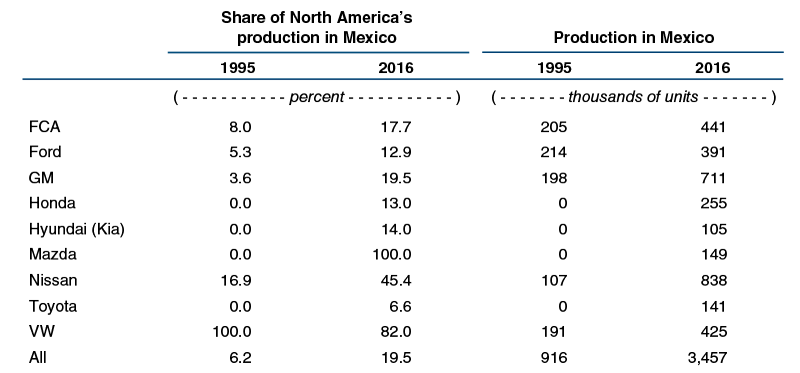
Source: Authors’ calculations based on data from WardsAuto InfoBank.
Mexico’s share of light vehicle production in North America is much higher than its share of light vehicle sales in the region. In 2016, Mexico produced about 3.5 million light vehicles, or 19.5 percent of North America’s total. By comparison, there were 1.6 million light vehicle sales in Mexico, or only 7.6 percent of the region’s total (). Mexico has just over 26 percent of North America’s population,18 so its share of the region’s sales is disproportionately low. While Mexico has featured a higher share of North America’s production than its sales for quite some time, the gap between the share of production and the share of sales became much more pronounced beginning around 2008. Mexico’s light vehicle production expanded rapidly, growing from 1.5 million units in 2009 to around 3.5 million in 2016, whereas its light vehicle sales increased more modestly from 753,000 in 2009 to 1.6 million over the same time period.19
Figure 2. Mexico’s share of North America’s light vehicle production and sales, 1990–2016
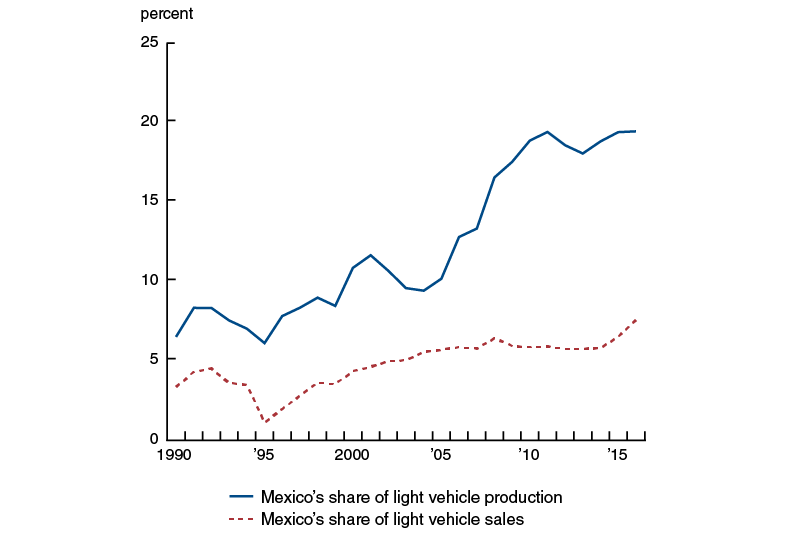
Since 2006, sales of new light vehicles in Mexico have been held down by a surge in the availability of used cars. A 2005 automotive decree from the Mexican government removed a number of barriers to the import of used cars from the United States. As a result, the number of used cars imported into Mexico essentially doubled—from 776,000 in 2005 to 1.6 million in 2006 (Iliff, 2016b). Mexico restored restrictions on the import of used cars in 2014 (Fry, 2014). Used car imports subsequently declined to 180,000 units in 2015, but nearly 8 million used cars had already been brought into the country between 2005 and 2015, depressing demand for new cars (Iliff, 2016b).
As Mexico’s economy has opened up, the share of imports among new light vehicles sold in the country has risen quite dramatically (see figure 3). Leading up to NAFTA, about 90 percent of new light vehicles sold in Mexico were produced in the country. Imports from the United States and Canada rose substantially during the 1990s. Subsequently, imports from other regions throughout the world (notably, those from Asia) have grown as well. For some time, the majority of new light vehicles sold in Mexico have been imported. In 2016, 56 percent of Mexico’s new light vehicle sales were produced in North America (41 percent in Mexico); that said, accounting for 25 percent of these sales, Asia was the region of origin with the second-largest share.
Figure 3. Mexico’s light vehicle sales, by region of origin, 1985–2016

Within North America, Mexico produces a distinct mix of light vehicles. To illustrate this, we group production data by vehicle segments. WardsAuto organizes vehicles into 28 segments. We consolidate those into ten segments—three for cars and seven for light trucks. The three segments for cars we distinguish are small, midsize, and large and luxury cars. The seven segments for light trucks are small crossover utility vehicles (CUVs), midsize CUVs, large and luxury CUVs, sport utility vehicles (SUVs), vans, small pickups, and large pickups. Automakers in Mexico specialize in two of these ten segments. In 2014, approximately one-half of Mexico’s light vehicle production was made up of small cars—and nearly one-fifth made up of large pickup trucks (table 4).20 Midsize cars and midsize CUVs each accounted for just under 10 percent of total production.
Table 4. Mexico’s light vehicle production, by vehicle segment, for select years
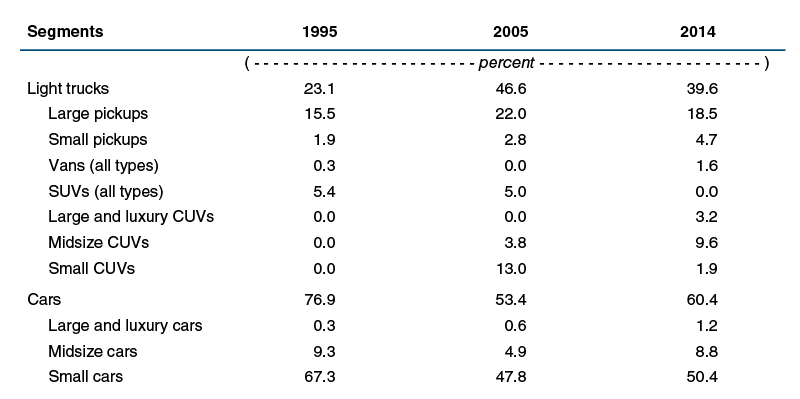
Source: Authors’ calculations based on data from WardsAuto InfoBank.
Note that Mexico’s vehicle production mix is not proportional to North America’s light vehicle sales mix. Rather, auto production in Mexico is quite specialized. In 2014, Mexico produced 48 percent of the small cars and 25 percent of the large pickups sold in North America (table 5). Mexico’s role in producing vehicles in these two segments for the North American market has been growing. Back in 2005, only 21 percent of small cars and 13 percent of large pickup trucks sold in North America were assembled in Mexico.21
Table 5. Mexico’s contribution to North America’s light vehicle sales, by vehicle segment, 2014

Sources: Authors’ calculations based on data from WardsAuto InfoBank and IHS Markit.
As seen in table 5, Mexico’s automotive production accounted for rather small shares of the vans, SUVs, and large and midsize cars—segments with declining sales—that were sold in North America in 2014. However, Mexico’s light vehicle output also accounted for fairly small percentages of the CUVs sold in the region that year; North America’s fastest-growing segment is CUVs (for which sales in the region more than doubled between 2005 and 2014, according to data from WardsAuto InfoBank).
The segmentation (or product mix) strategies vary among the five legacy producers in Mexico. Figure 4 shows them in three groups:
- As of 2014 Ford assembled only cars (chiefly small and midsize models) in Mexico. Ford no longer produces trucks in Mexico.
- FCA and GM specialize in large pickup trucks. These two companies were responsible for all of the large pickup truck production in Mexico in 2014; back then, 91 percent of FCA’s light vehicle production in Mexico and 98 percent of GM’s were large pickups (this output in Mexico represented 40 percent and 43 percent of FCA’s and GM’s full-size pickup production across North America, respectively).
- Nissan and VW primarily assemble small cars in Mexico. As of 2014, all that VW produced there was small cars, whereas Nissan also produced some small pickup trucks and vans in Mexico in addition to small cars.22
- Large pickup trucks represented 19 percent of production in Mexico in 2014 (see table 4). Two carmakers—FCA and GM—were responsible for producing all of them. Essentially all of the trucks were exported (97 percent); all but 3 percent of these exports from Mexico went to the United States or Canada.23
- Small cars, which represented 50 percent of Mexico’s production in 2014 (and 67 percent in 1995) (see table 4), were less likely to be exported north. Exports represented 77 percent of Mexico’s small car production in 2014, but only 65 percent of all these exports were shipped north to the United States and Canada. Furthermore, Detroit Three carmakers were responsible for producing only 16 percent of Mexico’s small cars in 2014 (down substantially from 56 percent in 1995).24
Figure 4 shows that automakers’ segmentation strategies in Mexico have not changed all that dramatically over the 20 or so years under NAFTA: Ford increased production of midsize cars, GM and FCA of large pickups, and VW and Nissan of small cars; GM’s and FCA’s respective decisions to start assembling CUVs in Mexico may be the only marked difference.
Figure 4. Mexico’s light vehicle production, by automaker and vehicle segment, 1995 and 2014
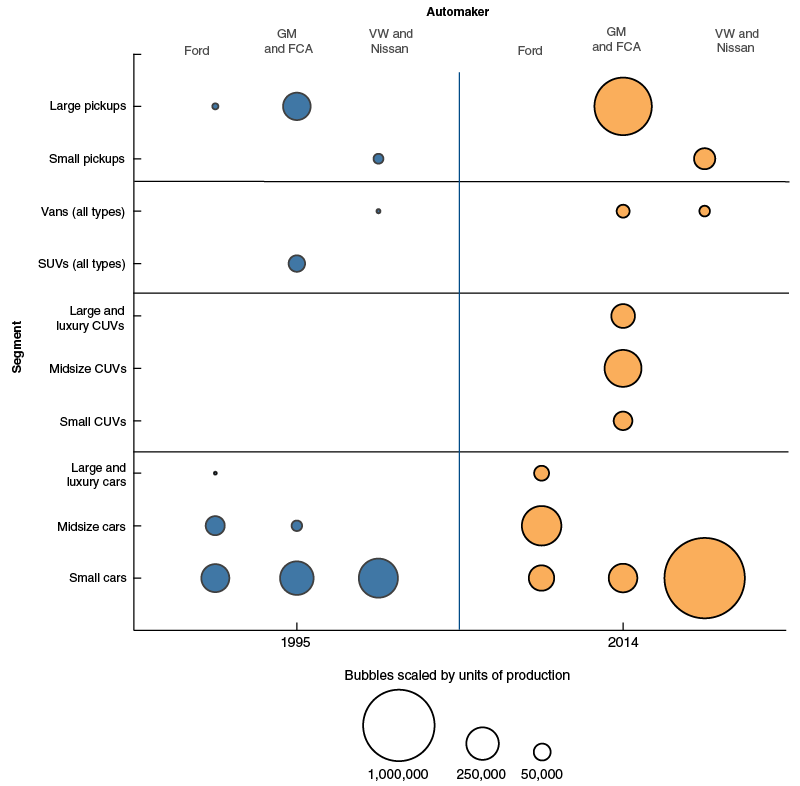
Source: Authors’ calculations based on data from WardsAuto InfoBank.
Mexico’s growing importance in automotive trade
Given the increasing gap between its automotive production and sales, Mexico inevitably is running a surplus in light vehicle trade. The share of Mexico’s light vehicle production that is exported increased from 14 percent in 1985 to 80 percent in 2016 (figure 5). Consistent with several decrees that emphasized trade liberalization for Mexico’s auto industry, exports started growing in the early 1980s. By 1994, when NAFTA came into effect, the export share had reached 53 percent. In 1995, that share shot up to 84 percent, representing the single biggest annual jump since 1985. Since 1995, exports have averaged 79 percent of Mexico’s production, with relatively little annual variation.25
Figure 5. Mexico’s volume of light vehicle exports and share of production exported, 1985–2016

How does Mexico’s auto export profile compare with those of the United States and Canada? We have access to data that document the country of destination for each vehicle model produced in Mexico for each year over the period 2005–14. The country of destination is unknown for approximately 10 percent of the vehicles, although after comparing the detailed data used in this article with aggregated data from WardsAuto InfoBank and AMIA, we are confident that “destination unknown” production can be classified as exports.26 In 2014 the United States exported only 21 percent of its vehicle production, whereas Mexico exported 82 percent and Canada 88 percent (table 6). Thus, less than 20 percent of light vehicles produced in Canada and Mexico are sold at home. Yet, compared with Canada’s light vehicle production, Mexico’s has a much broader set of destinations, with its NAFTA partners accounting for only 59 percent of it.27 Ninety-one percent of Canada’s light vehicle production remained in NAFTA; 79 percent of Canada’s light vehicle production went to its two NAFTA partners (the vast majority of which ended up in the United States).
Table 6. Light vehicle production in NAFTA countries, by destination, 2014
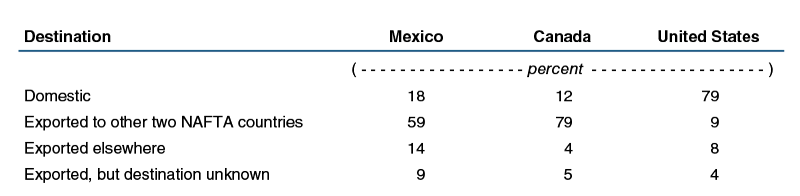
Source: Authors’ calculations based on data from IHS Markit.
Today most exports of light vehicles from Mexico head north. Identified exports to NAFTA partners (the United States and Canada) accounted for around 60 percent of vehicles produced in Mexico in 2005, 2010, and 2014 (table 7). Between 2005 and 2014, the shares of automotive production in Mexico going to Latin America and China increased, while the share of production sold domestically declined—from 26 percent to 18 percent.
Table 7. Mexico’s light vehicle production, by destination, for select years
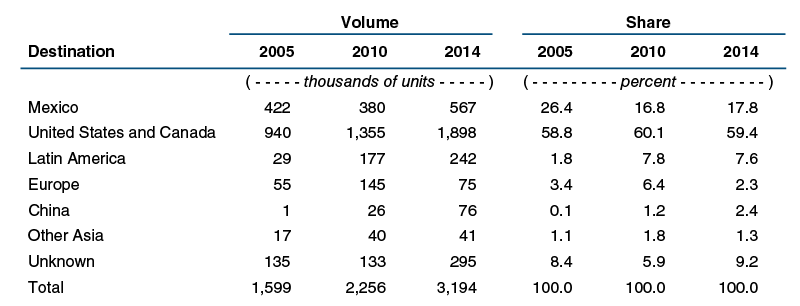
In 2014, each of the five legacy producers in Mexico exported a similar volume of light vehicles—around 400,000 to 500,000 units per producer (table 8). Each of the five companies accounted for between 17 and 22 percent of Mexico’s light vehicle exports. Newer entrants into Mexico (for instance, Honda, Mazda, and Toyota) were responsible for the remainder. FCA and Ford exported more than 90 percent of the vehicles they each produced in Mexico in 2014, whereas Nissan exported only 58 percent; for GM and VW, exports amounted to 82 percent and 85 percent, respectively.
Table 8. Light vehicle exports from Mexico, by automaker, 2014
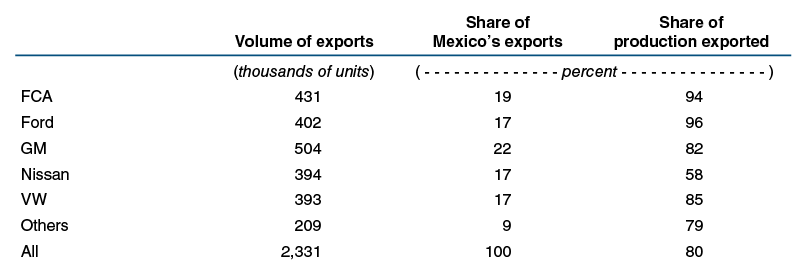
Source: Authors’ calculations based on data from IHS Markit.
Automakers differ by how much of their respective outputs in Mexico go to particular destinations (table 9). For four of the five legacy carmakers, on average, at least three-fourths of their light vehicle production in Mexico went to the United States and Canada or stayed in Mexico (that is, remained in the NAFTA region) in 2012–14. The exception was VW, which exported, on average, 38 percent of its light vehicle production in Mexico to the rest of the world (primarily Europe and, to some extent, South America) in 2012–14.
Table 9. Automakers, by destination of light vehicle production in Mexico, 2012–14 average
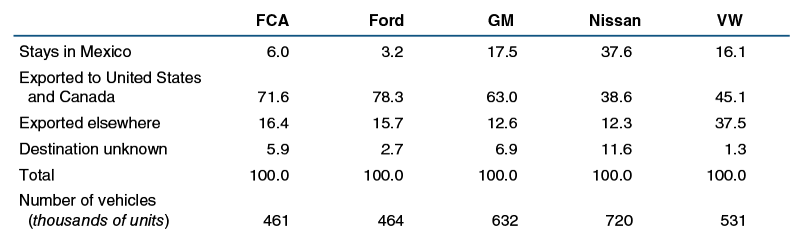
Source: Authors’ calculations based on data from IHS Markit.
Put another way, VW—which accounted for only 17 percent of light vehicle exports from Mexico in 2014 (see table 8)—was responsible for an annual average of 37 percent of Mexico’s production exported to regions outside North America over the period 2012–14 (table 10). In contrast, during 2012–14, Nissan accounted for an average of almost one-half of the light vehicles that were produced in Mexico and stayed there (table 10), although it produced only one-fourth of the vehicles in that country on average over that span.28
Table 10. Destination of light vehicle production in Mexico, by automakers, 2012–14 average
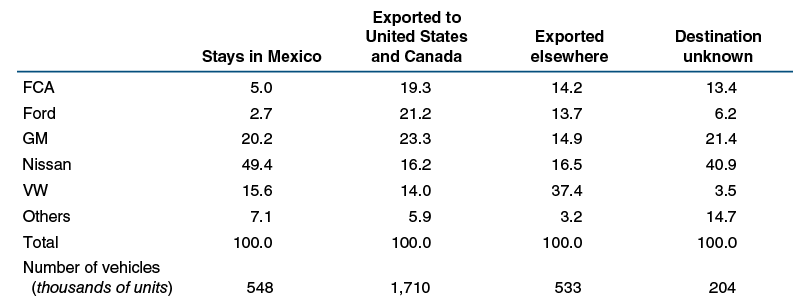
Source: Authors’ calculations based on data from IHS Markit.
Mexico’s growth in auto production and the industry’s footprint
How has the rapid growth of light vehicle production in Mexico altered the production footprint across the NAFTA region? In this section, we discuss the spatial distribution of the auto industry at two geographic scales: within Mexico and within North America.
Economic geographers consistently find that the motor vehicle industry has a high degree of agglomeration (Ellison and Glaeser, 1997; Duranton and Overman, 2005; and Goldman, Klier, and Walstrum, 2015). The motor vehicle industry has a tendency to agglomerate because of the co-location of the two types of production facilities: the several thousand producers of parts and the several dozen final assembly plants (where the parts are put together to make finished vehicles). In North America, most auto assembly plants and parts suppliers have traditionally clustered in a north–south corridor (chiefly in the United States) known as “auto alley.” A set of ten states that extend from Michigan south to the Gulf of Mexico makes up most of this corridor.29 This location pattern has arisen in large measure to minimize the cost of shipping finished vehicles to regional markets (Klier and Rubenstein, 2013a, 2015; Rubenstein, 1992; and Weber, 1929). Moreover, the pattern has emerged in part because it is common for parts plants to ship to multiple assembly plants, often run by different automakers (Klier and Rubenstein, 2008).
Agglomeration within Mexico
To accommodate the substantial increase in production in Mexico, carmakers have constructed numerous assembly plants there (table 11). In 1990, when NAFTA negotiations began, Mexico hosted eight active light vehicle assembly plants: Two of these were opened during the 1930s (by Chrysler and GM), four during the 1960s (by Chrysler, Ford, Nissan, and VW), and two during the 1980s (by Ford and GM). (Recall that Ford’s original plant in Mexico, opened in 1925, had already been closed by the mid-1980s.) In anticipation of NAFTA, four plants were opened during the first half of the 1990s (by Chrysler, GM, Honda, and Nissan) and GM’s 1930s-era plant was closed, which raised the total from eight to 11 by the end of the decade.
Table 11. Auto assembly plants in Mexico, 2016
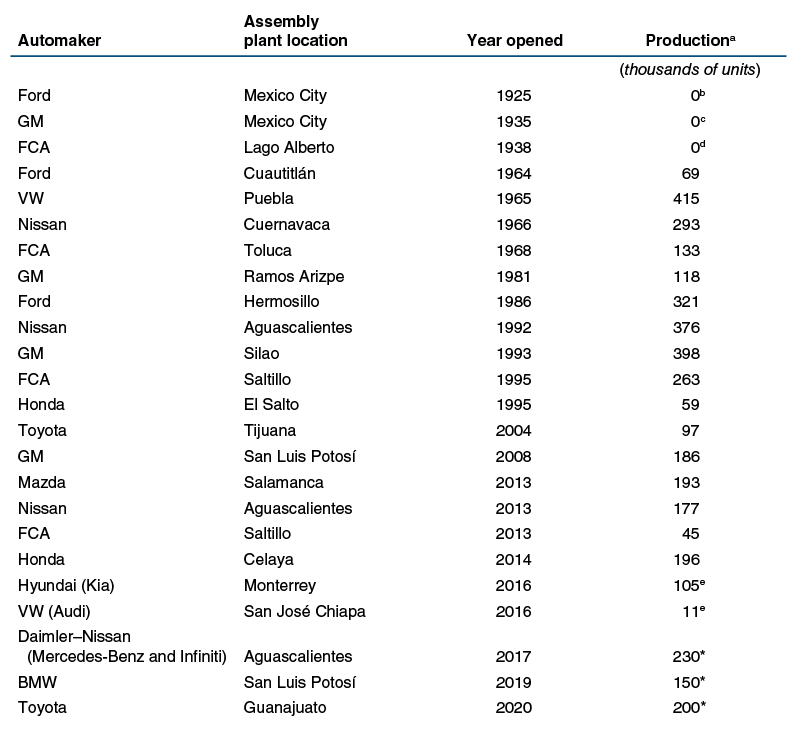
b Closed in 1984. (More details on this plant in note 6 of main text.)
c Closed in 1995.
d Closed in 2002.
e Partial year production.
*Anticipated (as of 2016).
Notes: This table shows all assembly plants as of 2016 for automakers that had been continuously producing vehicles in Mexico since they first entered the market. FCA means Fiat Chrysler Automobiles (pre-2014 data are only for Chrysler, which merged with Fiat in 2014). GM means General Motors. VW means Volkswagen. BMW means Bayerische Motoren Werke (Bavarian Motor Works). (GM also operated a low-volume truck plant in Toluca between 1995 and 2008; it produced a small number of commercial trucks, as well as full-size pickups.)
Sources: Healy (2016), Werner (1993), WardsAuto InfoBank, and company websites.
During the first decade of the twenty-first century, two plants were opened (by GM and Toyota) and the remaining 1930s-era plant was closed (by Chrysler), which brought the total to 12. During 2013 and 2014, four more assembly plants were opened (by Chrysler, Honda, Mazda, and Nissan). And then in 2016, two additional assembly plants were opened (by Hyundai Motor Group’s Kia Motors and VW’s Audi subsidiary). Three more plants were scheduled to open between 2017 and 2020 (two individually by BMW and Toyota, plus one jointly by Daimler’s Mercedes-Benz and Nissan’s Infiniti). Ford started construction on another plant in Mexico in 2016 but canceled it in 2017.30 Thus, the number of plants was slated to increase from 12 in 2012 to 21 in 2020, which would add 1.7 million units in light vehicle production capacity.31
Only one of the nine plants opened or set to open between 2010 and 2020 will have been constructed by the three Detroit-based automakers (specifically, Chrysler, in 2013) (see table 11). Five of the nine will have been constructed solely by Asian automakers, in order to source more of their North American small car sales from products made in North America rather than imports from Asia. The others will have been built by three German luxury auto manufacturers—VW’s Audi, BMW, and Daimler’s Mercedes-Benz (in conjunction with Nissan’s Infiniti). They have been drawn to Mexico because of the tariff savings on international sales of their premium vehicles produced there. In 2020, the Detroit Three producers are anticipated to operate only eight of 21 assembly plants in Mexico (see table 11). At 45 percent in 2016, the Detroit Three’s share of light vehicle production in Mexico is expected to decline in the coming years.32 By 2020, all of the 11 carmakers operating in Mexico will have other production facilities in North America. They tend to run their North American operations in a geographically integrated fashion. This applies especially to their respective supply chains, which extend across national borders in North America in many ways.
Within Mexico, agglomeration is especially noticeable. Vehicle production within Mexico is highly clustered in a rectangular area of about 50,000 square miles—which is around 150 miles east–west and 350 miles north–south, between Aguascalientes and San Luis Potosí on the northern end and between Cuernavaca, Cuautitlán, and Puebla on the southern end (figure 6).
Figure 6. Auto assembly plants and major railroads in Mexico, 2016

Sources: Authors’ adaptation of data from WardsAuto InfoBank, auto company websites, and Maptitude.
In 2016, 2.5 million light vehicles (or 72 percent of Mexico’s total light vehicle production) were assembled at 11 plants within this cluster. In 2020, around 3.3 million vehicles (about 73 percent of Mexico’s production) are anticipated to be produced at 15 assembly plants within this cluster.33
During the era of trade barriers, Mexico’s assembly plants and most parts production plants were clustered near Mexico City—the principal domestic market for vehicles. Starting in the late 1970s, the maquiladora motor vehicle parts plants were sited primarily in the north of Mexico, near the U.S. border, in order to minimize transportation costs to and from auto alley in the United States. Subsequently, three of the six assembly plants opened during the 1980s and the first half of the 1990s also located closer to the U.S. border.
Since the implementation of NAFTA, carmakers have returned to the traditional vehicle-producing region of central Mexico. In the twenty-first century, eight of the 11 assembly plants that opened or are set to open have been sited in central Mexico and only three have been sited in the north. Carmakers are locating in central Mexico in part to be in proximity to the country’s consumers (figure 7). About a quarter of the country’s population resides in and around Mexico City.34
Figure 7. Population density and auto assembly plants in Mexico
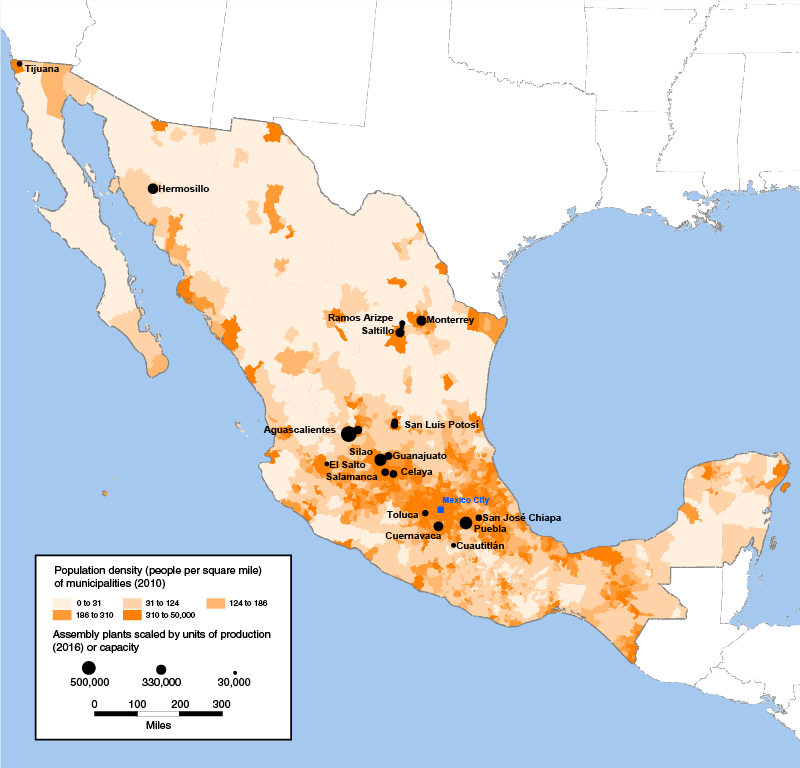
Sources: Authors’ adaptation of data from WardsAuto InfoBank, auto company websites, and Maptitude.
Also significant for the clustering of Mexico’s auto industry is the ease of access to the country’s transportation network, especially Class I railroads.35 An estimated 80–85 percent of motor vehicles assembled in Mexico and destined for the United States and Canada are transported by rail (Ludwig, 2016). When NAFTA implementation began, Mexico’s government-run rail system was not capable of meeting the needs of the auto industry’s just-in-time delivery model (Blanchard, 2013). In the mid-1990s, the government of Mexico privatized the rail system. The rail lines connecting the U.S. border with central Mexico were awarded to two railroads: Ferromex (Ferrocarril Mexicano) and Kansas City Southern de México (KCSM) (Douglas, 2012).36 Ferromex carries 55–60 percent of the vehicles assembled in Mexico to the U.S. border and KCSM 40–45 percent (Blanchard, 2013).37 These two railroads have invested heavily to improve service. As a result, for instance, KCSM reduced the time for the 700-mile run from Mexico City to Laredo, Texas, from 70 hours in 1996 to 34 hours in 2002 (Blaszak, 2013). The trains are equipped with bilingual computer screens and adapt easily to changes in the electric power grid (Blanchard, 2013).
Vehicles not exported by rail leave Mexico by sea. Figure 6 shows that some Class I rail lines run east–west to port cities on the coasts of the Gulf of Mexico and Pacific Ocean. Veracruz, on the Gulf Coast, handles approximately 80 percent of Mexico’s vehicle exports. Most of the remainder leave through Lázaro Cárdenas on the country’s west coast (Swiecki and Menk, 2016, p. 27). VW operates a fleet of six “ro-ro” (roll-on, roll-off) ships on a triangular trade route. Vehicles made in Germany are loaded at the port of Emden, and unloaded at Veracruz for sale in Mexico. The ships are then reloaded with VW vehicles assembled in Puebla; some are unloaded at ports on the U.S. East Coast, whereas others stay on the ships as they return to Europe (Blaszak, 2013).
Note that within Mexico’s auto assembly cluster, vehicles destined for countries other than the United States and Canada tend to be produced in plants closer to Veracruz, the main shipping port for finished vehicles. Figure 8 shows that the correlation between the distance of assembly plants in Mexico to Veracruz and the share of exports from each of these plants that goes to non-NAFTA countries is –0.24 in 2014 (in other words, the farther away a plant is from Veracruz, the lower is its share of production bound for non-NAFTA destinations).
Figure 8. Correlation between distance to Veracruz and export share to non-NAFTA countries, 2014
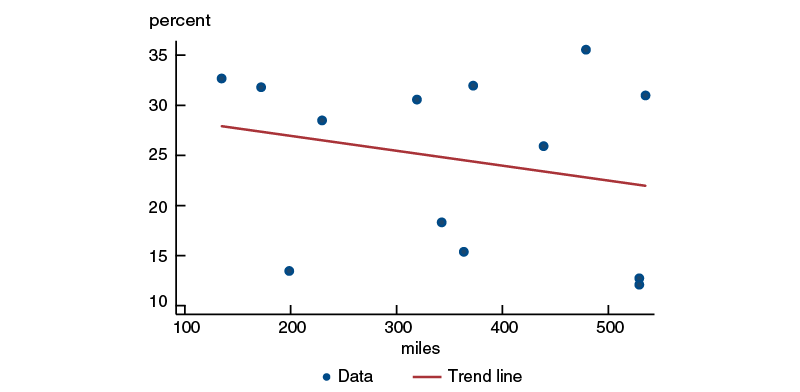
Sources: Authors’ calculations based on data from IHS Markit and Maptitude.
Agglomeration within North America
Given the significant changes in Mexico’s light vehicle production and exports under NAFTA, we are left to wonder whether the economic geography of auto production across the wider North American region is being fundamentally restructured. In other words, what does the growing role of Mexico in auto manufacturing imply for the industry’s economics and spatial distribution within North America?
In 1995, shortly after NAFTA implementation began, 84 percent of the light vehicles sold in the United States were assembled in one of the three North American countries. By 2016, that share had slipped a bit to 78 percent.38 In other words, the vast majority of light vehicles sold in the United States continue to be produced in North America. However, within North America, the distribution of assembly plants has changed quite a bit over the past two decades.
In 2014, 79 percent of light vehicles sold in the U.S. market were produced in North America (see table 12). The balance was imported from Asia (14.6 percent) and Europe (6.4 percent). Of the vehicles produced in North America and sold in the United States, 69 percent were produced in the United States, 14 percent in Canada, and 13 percent in Mexico (with 4 percent not being attributed in the data).39
Table 12. Light vehicle sales in the United States, by region of origin, 2014
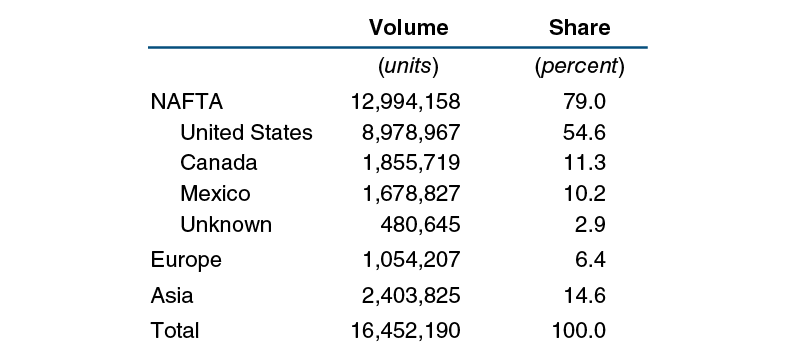
Sources: Authors’ calculations based on data from WardsAuto InfoBank and IHS Markit.
To date, the increases in Mexico’s volume and share of North America’s light vehicle production have not come at the expense of the existing production in auto alley—which remains the principal cluster of production, with nearly three times the production volume of Mexico’s. Between 1995 and 2016 auto alley actually increased its share of North America’s light vehicle production—by 2.8 percentage points—as the overall volume of industry production in the NAFTA region jumped by 2.8 million units. Mexico’s growth has come principally through the shuttering of assembly plants in the United States outside of auto alley, as well as, to a smaller extent, in Canada (see table 13 and figures 9 and 10).
Table 13. Light vehicle production, by location within North America, 1995 and 2016
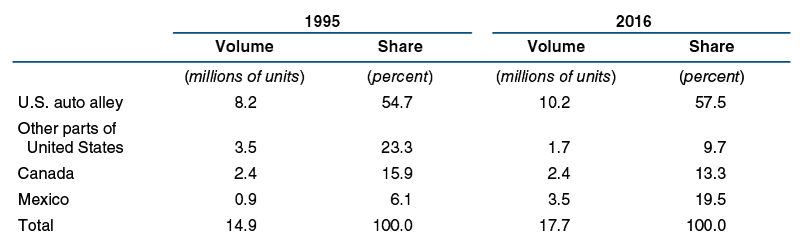
Source: Authors’ calculations based on data from WardsAuto InfoBank.
Figure 9. North America’s light vehicle production footprint, 1995
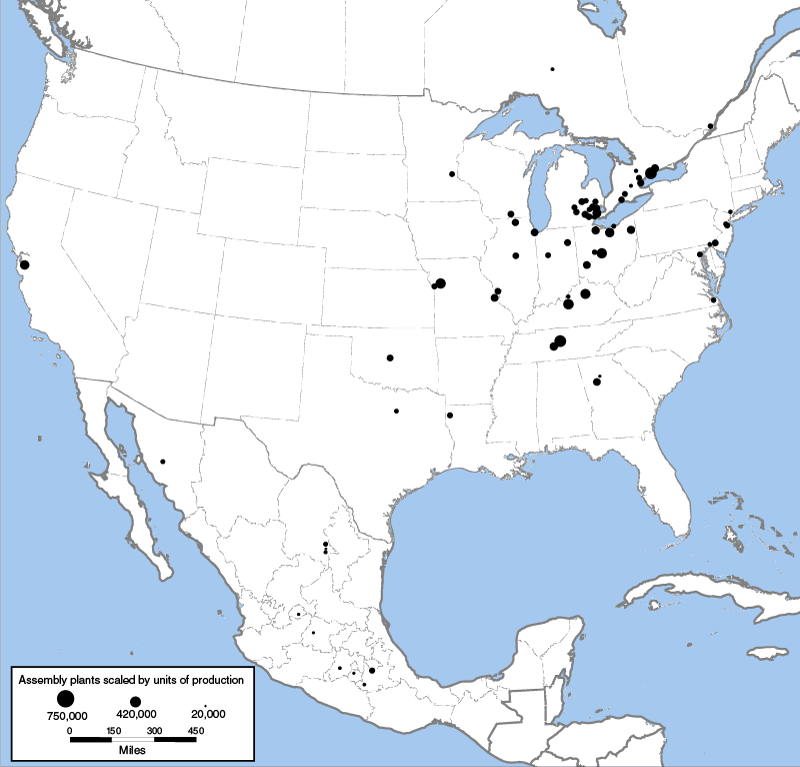
Figure 10. North America’s light vehicle production footprint, 2016
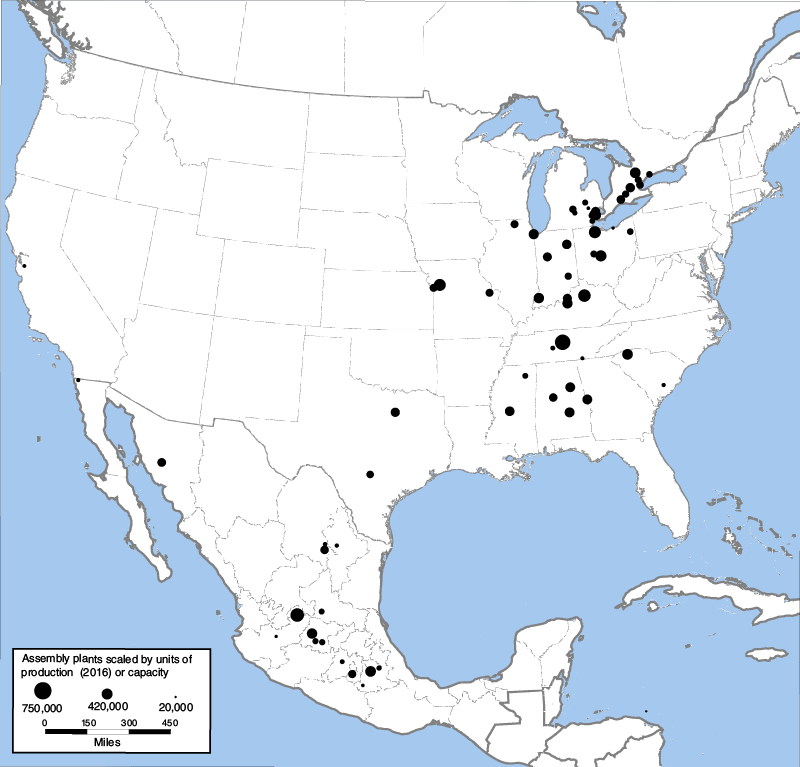
Sources: Authors’ adaptation of data from WardsAuto InfoBank, auto company websites, and Maptitude.
As we’ve already documented, a second significant cluster has formed within Mexico, in addition to auto alley in the United States (and Canada). So, there are now two major auto production clusters within North America. Mexico’s share of North America’s light vehicle production increased from a little over 5 percent to almost 20 percent during the first two decades of NAFTA (figures 1 and 2), and nearly 60 percent of its production was sent to its NAFTA neighbors to the north in 2014 (table 6). As a result, relative to the mid-1990s, when NAFTA implementation commenced, far more vehicles are now being transported over longer distances from assembly plants to dealers. The Center for Automotive Research (CAR) estimates that, for the case of a midsize car, carmakers incur an average of $900 more in shipping costs for a vehicle produced in Mexico and sold in the U.S. market, compared with one produced and sold in the United States (Swiecki and Menk, 2016, p. 46). CAR also estimates that labor costs for final assembly are on average $600 lower and parts production costs $1,500 lower in Mexico than in the United States (Swiecki and Menk, 2016, p. 46). Thus, according to CAR, carmakers are now realizing net savings by locating production of some types of vehicles in Mexico, largely because of much lower parts production costs in Mexico versus the United States.40 These net savings help explain why Mexico now hosts North America’s second cluster of auto production.
Finally, on account of its central location between the United States and South America, Mexico has the potential to play a prominent role in automotive production across the entire Western Hemisphere. The clustering of assembly plants in central Mexico, rather than along the U.S. border, allows these plants to more easily export vehicles to South America. If southbound trade were to increase, Mexico’s auto production cluster could be further strengthened.
Conclusion
The implementation of NAFTA, which began in 1994, deepened the integration of Mexico into the North American economic space. Mexico’s light vehicle assembly and share of North America’s production have grown rapidly during the past quarter-century. Most of the increase in auto output has been exported, with the United States remaining the principal destination, although other destinations have been accounting for growing shares. In 2014, around 83 percent of Mexico’s light vehicle production was exported, compared with about 76 percent in 2005 (figure 5). Meanwhile, the share of Mexico’s production sold in Mexico declined from 26 percent in 2005 to 18 percent in 2014 (table 7).
Light vehicle production and exports from Mexico have been concentrated in two vehicle segments: large pickups and small cars. Assembly plants opened or under construction during the 2010s have been designed primarily for the production of small cars.
Five foreign-headquartered automakers—FCA (formerly Chrysler), Ford, GM, Nissan, and VW—have long dominated light vehicle production in Mexico as a result of a lack of domestic producers and a succession of government decrees regulating local car content. Following the elimination of trade barriers within North America, these five legacy automakers have adopted different product mixes and export strategies. Furthermore, a number of international carmakers have added production capacity in Mexico (some, such as Mazda, for the first time) since the turn of the millennium; much of the output of these producers represents a substitution of imports to North America from Asia. In addition, the three leading German-owned premium brands (VW’s Audi, BMW, and Daimler’s Mercedes-Benz) have also been attracted to Mexico because it gives these automakers the ability to export high-priced vehicles to a large number of countries without facing tariffs, thanks to the Mexico’s large number of free trade agreements.
To date, Mexico’s rapid growth in auto output has not come at the expense of production within the U.S. corridor dubbed auto alley. However, the rise of Mexico’s auto industry represents the emergence of a second vehicle production cluster within North America. The assembly plants within this cluster tend to specialize in making small cars and large pickups, and they are well positioned to export their vehicles throughout the Western Hemisphere.
Notes
1 Mexico’s auto production and export data cited here are from WardsAuto InfoBank, database available online by subscription, and AMIA (Asociación Mexicana de la Industria Automotriz, or, in English, Mexican Automotive Industry Association), available online by subscription (accessed April 10, 2017). In this article, we focus on light vehicle production—that is, the production of passenger cars and light trucks; we exclude from our analysis medium- and heavy-duty trucks (such as those used in the construction industry) and buses.
2 More specifically, Mexico had 61,100 workers in vehicle assembly and 674,372 in parts production in 2016; these data are from INEGI (Instituto Nacional de Estadística y Geografía, or, in English, National Institute of Statistics and Geography), available online (accessed June 20, 2017). By comparison, employment in the U.S. motor vehicle industry totaled 760,800 in 2016 (180,900 in vehicle assembly and 579,900 in parts production); these data are from the U.S. Bureau of Labor Statistics from Haver Analytics.
3 Swiecki and Menk (2016, p. 32).
4 Ruda (2016).
5 In this article, we refer to the NAFTA region and North America interchangeably for convenience. We focus on just the integration of the motor vehicle assembly sector within the NAFTA region, and do not discuss what has happened with the motor vehicle parts sector across the region. By “intra-industry trade,” we mean trade in similar products (often differentiated by the level of quality and/or particular features) between nations. We also don’t discuss what might happen if the North American Free Trade Agreement were to be changed (see, for example, Dziczek et al., 2017).
6 See Healy (2016, p. 41) and Werner (1993). In 1925 Ford started assembling its Model Ts in a rented garage (its first plant) near downtown Mexico City. (In 1932, the company built a plant from the ground up in another part of Mexico City and moved its operations there.)
7 From this point on, unless indicated otherwise, references to (actual and planned) assembly plant openings (and closings), as well as light vehicle production, are taken straight from auto company websites; WardsAuto InfoBank; and Ramírez de la O (1998).
8 The other two original plants owned by the Detroit Three were closed much later—in 1995 (GM’s) and 2002 (Chrysler’s).
9 Precipitated by plummeting oil revenues, the value of the Mexican peso fell from 26 to around 3,000 to the U.S. dollar between 1982 and 1987 (Hayes, 1987).
10 To be able to sell their output in Mexico, auto firms not already producing there when NAFTA began had to have around 30 percent of their vehicles’ parts originate in that country; however, this onerous requirement for new entrants was phased out by 2003 (Womack, 1994, note 5, p. 18).
11 The light vehicle production and sales percentage values are from authors’ calculations based on data from WardsAuto InfoBank.
12 Authors’ calculations based on data from WardsAuto InfoBank.
13 Authors’ calculations based on data from WardsAuto InfoBank.
14 Chrysler was fully merged with Fiat in 2014, forming Fiat Chrysler Automobiles. For Chrysler’s history, visit the website.
15 Authors’ calculations based on data from WardsAuto InfoBank.
16 We use these start dates for particular reasons: The year 1995 corresponds roughly to when NAFTA implementation began, 1990 is when NAFTA negotiations commenced, and 2010 marks the first full year following the end of the Great Recession.
17 Authors’ calculations based on data from WardsAuto Forecasts, database available online by subscription,(projections as of August 2017).
18 Authors’ calculations based on data from the Population Reference Bureau (2016).
19 Mexico’s yearly totals for both light vehicle production and sales mentioned throughout this paragraph are from WardsAuto InfoBank.
20 By 2016 those percentages were little changed; we focus here on 2014 production data, since we later introduce data on export destinations. Among the sources we have access to, those export data are available only through 2014.
21 Authors’ calculations based on data from WardsAuto InfoBank and IHS Markit.
22 Authors’ calculations based on data from WardsAuto InfoBank.
23 Authors’ calculations based on data from IHS Markit.
24 Authors’ calculations based on data from WardsAuto InfoBank and IHS Markit.
25 Authors’ calculations based on data from WardsAuto InfoBank and AMIA.
26 That means the values for the specific export destinations (and origins of imports) listed in tables 6, 7, 9, 10, and 12 represent lower bounds.
27 That is the minimum share of Mexico’s light vehicle production exported to its NAFTA partners; if all exports whose destinations are unknown were sent to the United States and Canada, the share could be as high as 68 percent (see table 6).
28 Authors’ calculations based on data from WardsAuto InfoBank.
29 Auto alley is the defined as the area within 100 miles of the U.S. interstate highways I-65 and I-75. It includes assembly plants within the ten states of Alabama, Georgia, Illinois, Indiana, Kentucky, Michigan, Mississippi, Ohio, South Carolina, and Tennessee. Auto alley is sometimes defined to extend into the southern end of Ontario, Canada, along Route 401.
30 Ford’s decision in early 2017 to cancel construction of an assembly plant to be built in Mexico reflected the company’s recognition that it could meet demand for small and midsize cars from existing assembly plants (Woodall and Shepardson, 2017).
31 Authors’ calculations based on data from WardsAuto InfoBank and WardsAuto Forecasts (projections as of August 2017).
32 Authors’ calculations based on data from WardsAuto InfoBank and WardsAuto Forecasts (projections as of August 2017).
33 Authors’ calculations based on data from WardsAuto InfoBank and WardsAuto Forecasts (projections as of August 2017).
34 Information from entry on Mexico in the CIA World Factbook, available online.
35 A Class I railroad in the United States is defined by the Surface Transportation Board as having annual carrier operating revenues of $457.91 million or more in 2015. Two Mexican railroads, Ferromex (Ferrocarril Mexicano) and Kansas City Southern de México (KCSM), meet the U.S. definition (Association of American Railroads, 2017).
36 The United States has seven Class I railroads, and Canada has two that meet the U.S. definition of Class I railroads (Association of American Railroads, 2017).
37 For example, most vehicles shipped by KCSM from Mexico are transferred at terminals inside the United States to one of seven U.S. Class I railroads or one of two Canadian Class I railroads (not all Class I railroads transport light vehicles)—to Union Pacific (UP) at Laredo, Texas; to UP, Canadian Pacific, and CSX at Kansas City, Missouri; to Canadian National at Jackson, Mississippi; to Norfolk Southern at Meridian, Mississippi; and to BNSF at Fort Worth, Texas. VW transfers most of its vehicles assembled in Puebla from Mexican to U.S. trains at a facility in Houston, Texas (Blanchard, 2013).
38 Authors’ calculations based on data from WardsAuto InfoBank.
39 Authors’ calculations based on data from WardsAuto InfoBank and IHS Markit.
40 Swiecki and Menk (2016) reached a different conclusion than a similar comparison by the U.S. Congress, Office of Technology Assessment (1992) did 24 years earlier. Perhaps this is not all that surprising given how much time had passed. Back in the early 1990s, higher costs for producing parts in Mexico and for shipping finished vehicles from Mexico (relative to these costs for plants in the United States) more than outweighed a modest labor cost saving, according to the OTA. Thus, in 1992 the OTA concluded that labor cost savings from auto production in Mexico were less than the shipping penalty (U.S. Congress, Office of Technology Assessment, 1992, p. 145; and Studer, 1994, pp. 30–31). According to Swiecki and Menk (2016, p. 48), the 1992 OTA data on transportation and labor costs was “integral” in securing passage of NAFTA in the United States as these data suggested that the competitive position of the U.S. auto industry was secure.
References
Association of American Railroads, 2017, “Class I railroad statistics,” report, Washington, DC, May 1, available online.
Berry, Steven, Vittorio Grilli, and Florencio López-de-Silanes, 1992, “The automobile industry and the Mexico - US free trade agreement,” National Bureau of Economic Research, working paper, No. 4152, August, available online.
Blanchard, Roy, 2013, “Kansas City Southern bets big on Mexico,” Trains, Vol. 73, No. 11, November, pp. 66–71.
Blaszak, Michael W., 2013, “Riding the auto traffic boom,” Trains, Vol. 73, No. 11, November, pp. 24–33.
De La Cruz, Justino, Robert B. Koopman, Zhi Wang, and Shang-Jin Wei, 2011, “Estimating foreign value-added in Mexico’s manufacturing exports,” U.S. International Trade Commission, Office of Economics, working paper, No. 2011-04A, April, available online.
Douglas, Merrill, 2012, “In Mexico, rail is on a roll,” Inbound Logistics, January 15, available online.
Duranton, Gilles, and Henry G. Overman, 2005, “Testing for localization using micro-geographic data,” Review of Economic Studies, Vol. 72, No. 4, October, pp. 1077–1106.
Dziczek, Kristin, Bernard Swiecki, Yen Chen, Valerie Brugeman, Michael Schultz, and David Andrea, 2017, “NAFTA briefing: Trade benefits to the automotive industry and potential consequences of withdrawal from the agreement,” Center for Automotive Research, January, available online.
Ellison, Glenn, and Edward L. Glaeser, 1997, “Geographic concentration in U.S. manufacturing industries: A dartboard approach,” Journal of Political Economy, Vol. 105, No. 5, October, pp. 889–927.
Fry, Steven M., 2014, “New rules announced for permanently importing used cars into Mexico,” Surviving Yucatan, blog, September 17, available online.
Goldman, Benjamin, Thomas H. Klier, and Thomas Walstrum, 2015, “The agglomeration of R&D and production activities among research-intensive manufacturers,” paper presentation at iBEGIN (International Business, Economic Geography and Innovation) Conference, Temple University, Fox School of Business, Center for International Business Education and Research (CIBER), Philadelphia, November 14.
Hayes, Thomas C., 1987, “Mexico’s border plants thrive on weak peso,” New York Times, November 23, available online.
Healy, Teresa, 2016, Gendered Struggles against Globalisation in Mexico, Abingdon, UK: Routledge.
Hufbauer, Gary Clyde, and Jeffrey J. Schott, 2005, NAFTA Revisited—Achievements and Challenges, Washington, DC: Peterson Institute for International Economics.
Iliff, Laurence, 2016a, “Booming Mexico output squeezes suppliers,” Automotive News, Vol. 90, No. 6741, September 5, p. 4.
Iliff, Laurence, 2016b, “Undoing NAFTA’s unintended effect,” Automotive News, July 18, available online.
Klier, Thomas H., and James M. Rubenstein, 2015, “Auto production footprints: Comparing Europe and North America,” Economic Perspectives, Federal Reserve Bank of Chicago, Vol. 39, Fourth Quarter, pp. 101–119, available online.
Klier, Thomas H., and James M. Rubenstein, 2013a, “The evolving geography of the US motor vehicle industry,” in Handbook of Industry Studies and Economic Geography, Frank Giarratani, Geoffrey J. D. Hewings, and Philip McCann (eds.), Cheltenham, UK: Edward Elgar, pp. 38–66.
Klier, Thomas H., and James M. Rubenstein, 2013b, “The growing importance of Mexico in North America’s auto production,” Chicago Fed Letter, Federal Reserve Bank of Chicago, No. 310, May, available online.
Klier, Thomas H., and James M. Rubenstein, 2008, Who Really Made Your Car? Restructuring and Geographic Change in the Auto Industry, Kalamazoo, MI: W. E. Upjohn Institute for Employment Research.
Ludwig, Christopher, 2016, “In-depth analysis: Strong logistics and supply base central to Ford’s new Mexico plant,” Automotive Logistics, April 6, available online
Moreno Brid, Juan Carlos, 1996, “Mexico’s auto industry after NAFTA: A successful experience in restructuring?,” University of Notre Dame, Helen Kellogg Institute for International Studies, working paper, No. 232, August, available online.
Moreno Brid, Juan Carlos, 1992, “Structural change in Mexico’s motor vehicle industry (1977–89),” in Industry on the Move: Causes and Consequences of International Relocation in the Manufacturing Industry, Gijsbert van Liemt (ed.), Geneva, Switzerland: International Labour Office, pp. 259–278.
Murphy, Fidelma, and Terrence McDonough, 2012, “US auto companies’ ownership and control of production in Mexico’s ‘maquiladoras,’” Cambridge Journal of Regions, Economy and Society, Vol. 5, No. 3, November, pp. 413–434.
Population Reference Bureau, 2016, “2016 world population data sheet,” Washington, DC, available online.
Ramírez de la O, Rogelio, 1998, “The impact of NAFTA on the auto industry in Mexico,” in The North American Auto Industry under NAFTA, Sidney Weintraub and Christopher Sands (eds.), Washington, DC: CSIS (Center for Strategic and International Studies) Press, pp. 48–91.
Rice, Justin Gazer, 1998, “PITEX and maquiladora import programs: A working guide and comparative evaluation,” Texas International Law Journal, Vol. 33, No. 2, Spring, pp. 365–380.
Rubenstein, James M., 1992, The Changing US Auto Industry: A Geographical Analysis, London and New York: Routledge.
Ruda, Taneli, 2016, “Trade trends: Mexico’s auto plan,” American Shipper, May 24, available online.
Russell, Philip L., 2016, The Essential History of Mexico: From Pre-Conquest to Present, New York and Abingdon, UK: Routledge.
Studer, Isabel, 1994, “The impact of NAFTA on the Mexican auto industry,” North American Outlook, Vol. 5, November, pp. 20–55.
Swiecki, Bernard, and Debbie Maranger Menk, 2016, “The growing role of Mexico in the North American automotive industry: Trends, drivers and forecasts,” Center for Automotive Research, report, July, available online.
U.S. Congress, Office of Technology Assessment, 1992, U.S.-Mexico Trade: Pulling Together or Pulling Apart?, report, No. ITE-545, Washington, DC: U.S. Government Printing Office, October.
Villarreal, M. Angeles, 2017, “Mexico’s free trade agreements,” CRS Report for Congress, Congressional Research Service, No. R40784, April 25.
Weber, Alfred, 1929, Alfred Weber’s Theory of the Location of Industries, Carl Joachim Friedrich (trans. and ed.), Chicago: University of Chicago Press.
Werner, Johannes, 1993, “68 years of feast or famine,” Automotive News, Vol. 67, No. 5519, September 27, p. 37.
Wilson, Patricia A., 2010, “Maquiladoras,” in Handbook of Texas Online, Texas State Historical Association, entry uploaded June 15, available online.
Womack, James P., 1994, “The North American auto industry under NAFTA: Making the positive sum solution happen,” North American Outlook, Vol. 5, November, pp. 3–19.
Womack, James P., Daniel T. Jones, and Daniel Roos, 1991, The Machine That Changed the World: The Story of Lean Production, New York: Harper Perennial.
Woodall, Bernie, and David Shepardson, 2017, “Ford scraps plan for $1.6 billion plant in Mexico after Trump criticism,” Reuters, January 3, available online.