The following publication has been lightly reedited for spelling, grammar, and style to provide better searchability and an improved reading experience. No substantive changes impacting the data, analysis, or conclusions have been made. A PDF of the originally published version is available here.
From the steel industry to the retail industry, from Caterpillar to General Motors, the Midwest has faced a dramatically changing environment during the past decade or more. In its initial response, the region seemed headed into a tailspin of plant closings and displaced workers. Now, however, some businesses are regaining market share, perhaps in part because they adjusted quickly to change as it occurred. Other businesses have been less fortunate and are still struggling to find their way.
To some degree, the automotive industry reflects the economic changes of the region and the nation as a whole over the last decade. Not all automakers have been equally successful in adapting to change. Yet the adjustment process is not finished, and much remains to be done before the full ramifications become clear. This Fed Letter reviews the recent experience of the auto industry and the ways in which its responses to change have affected the Midwest economy.
The transformation of an industry
The challenges that the domestic auto industry faces today are not new; in fact, they have been widely documented over the past 20 years.1 Prior to that time, the U.S. auto marketplace was insulated and dominated by the “Big Three”—Chrysler, Ford, and General Motors (GM). This arrangement was disrupted by a series of rude awakenings, particularly the energy crisis that began in the mid-1970s and the strong dollar in the mid-1980s. Suddenly, aggressive foreign challengers were permanently penetrating the U.S. marketplace. Through the late 1970s and 1980s, Big Three hegemony crumbled. In response, Big Three employment dropped by about 35% (see figure 1). By 1990, one of every three cars sold in the U.S. bore a foreign nameplate.2
1. Employment in Big Three
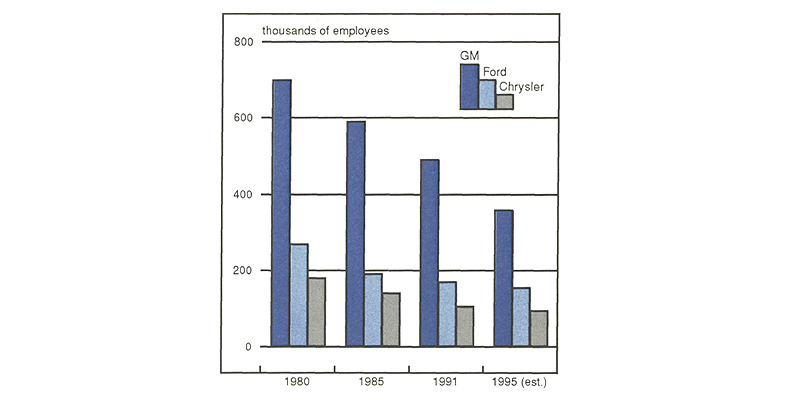
The foreign competitors used effective new production methods, such as lean manufacturing and a shorter time from design to production, that combined with other factors to give them an overwhelming cost advantage over the Big Three.3 In addition, they offered an increasing variety of models, better customer service, and higher product quality. All these features wooed customers away from the Big Three and accelerated the erosion of Big Three market share.
Faced with these realities, the Big Three reacted in varying ways. An initial response came in the early 1980s. Ford and Chrysler—the latter facing a real possibility of bankruptcy—aggressively began streamlining domestic operations. Both firms pared back employment significantly, reduced capacity, and poured funding into research and development, specifically product development. By the mid-1980s, Ford was successfully using lean production techniques, and by the end of the decade, cost control and reduction had become a way of life at both companies. Overall, Ford and Chrysler significantly improved productivity during the period (see figure 2). The brisk economic recovery of the 1980s also improved the balance sheets of both firms and helped facilitate their transition.
2. Productivity gains by Big Three
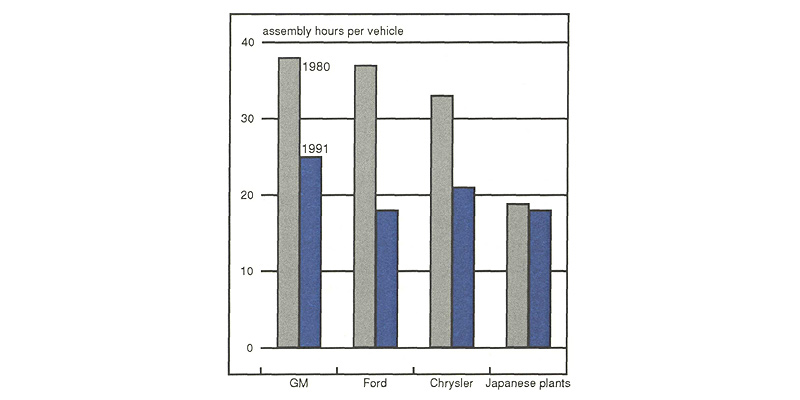
Unlike Chrysler, GM did not face the ominous threat of bankruptcy. This may help explain why early on, GM did less than Ford or Chrysler to pare costs and to reduce employment and capacity. Significant cash reserves also helped brighten GM’s outlook. So did a sales recovery and the company’s maintenance of a market share in excess of 40% from 1979 through the early 1980s. GM did improve productivity, but not to the same degree as Chrysler or Ford. Then, starting in the mid-1980s, the company’s market share began slipping. In 1991, problems came to a head. GM’s losses for the year totaled $4.45 billion; losses in the company’s core North American operations were estimated at more than $7 billion.
GM has now taken drastic action to address these losses and reduce overcapacity given its drop in market share. In late 1991, the company announced it would close approximately 28 plants and eliminate over 75,000 jobs. Among the targets were four assembly plants and more than 20,000 white-collar jobs. Cost-cutting measures were also in the works, including reductions in health benefits and in research and development.
Unfortunately, even these aggressive actions did not solve the problems of the world’s largest corporation. Media headlines over the past year have documented the turmoil of GM plant closings, massive losses, and boardroom coups. After incurring a 1992 loss in North America of perhaps $4 billion, the company announced its latest boardroom realignments and plans for more cost-cutting. GM will reduce the number of model lines, cut the costs of parts, and sell or close numerous parts facilities. Such events have spelled trauma in the past for a proud company and a key Midwest industry; they are likely to cause hardships into the 1990s.
Restructuring can pay dividends
Restructuring is always painful, yet it can yield valuable benefits. Struggling to meet the competition, American automakers have adopted new technologies and lean production methods. Additionally, the industry has pushed ahead with development processes and is shifting to agile production techniques, which combine lean production methods with greater flexibility of output. The benefits of these changes have shown up in the finished products, namely, the highly praised new models rolling out of American assembly plants. Since the mid-1980s, the industry has made great strides in product quality, and American cars now approach world-class standards of quality.
At the same time, surveys show surprising improvements in customer service among the Big Three relative to their competitors. Together, they still lag behind Japanese automakers. Yet customer service at Ford and Chrysler matches and, in some car lines, actually exceeds that of Japanese nameplates. A complementary development has been the rapid integration of production activities within North America and the expansion of activities of American automakers in European markets.
Productivity has also improved. In 1979, Big Three productivity was significantly below that of foreign automakers; by 1991, the gap had narrowed substantially (see figure 2). By some measures, Ford is now one of the most efficient producers in the world. After significant improvements at Chrysler, its productivity also matches that of many other producers in the world.
Inevitably, more restructuring lies ahead for domestic automakers. Yet it need not be as traumatic as it was in the past. Because the industry has changed since 1979, automakers should be better positioned to meet the challenges of the marketplace. Recent market share gains of the Big Three relative to foreign nameplates mean that domestic companies have at least temporarily stopped their downward slide. And although the outlook for the industry is highly competitive, Ford and Chrysler seem likely to survive and even prosper
GM is still grappling with some of the problems it faced in the 1980s. Yet the company continues to have significant potential, and its current restructuring should transform it into a leaner, more aggressive competitor. The new Saturn has been a success for GM, and Pontiac, Buick, Oldsmobile, and Cadillac also boast trend-setting new models. Thus, even GM is showing signs of being a market leader in some segments and a world-class competitor in its production technology.
The impact of auto industry restructuring on the Midwest
Given the concentration of auto manufacturing in the Midwest, the industry’s restructuring has affected the region most directly. In the late 1980s and early 1990s, assembly plants in the Midwest (including Ohio) produced over 60% of all cars in the U.S. (see figure 3). Counting assembly, parts, and support facilities of Big Three and foreign automakers, more than 500,000 Midwest workers are employed in the auto industry. External suppliers and related industries boost that number to between 1.25 and 1.5 million jobs. These estimates do not include the jobs directly and indirectly supported by the industry, especially in the service sector.4
3. Car assembly plant locations—1992
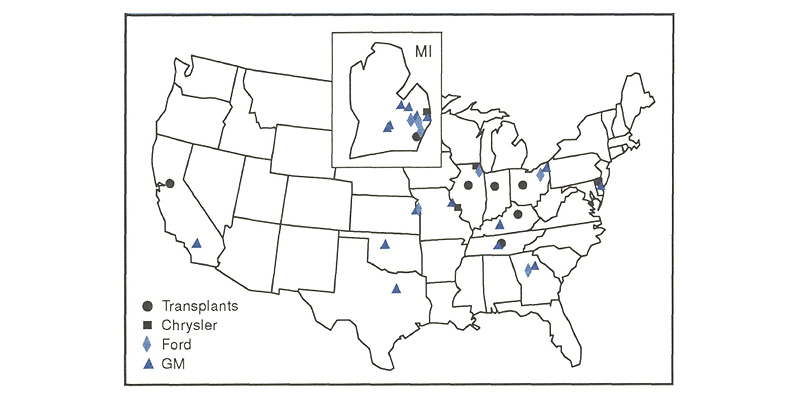
Such numbers make clear that the auto industry still looms large in the Midwest, yet it looms less large than in the past. Since 1979, for instance, Michigan has lost over 200,000 auto-related production jobs; the Big Three have been responsible for about three-fourths of that reduction. In fact, job cuts have been striking across the Big Three. Between 1979 and 1991, GM cut 39% if its production jobs, Ford 33%, and Chrysler 42%. Cuts such as these are of course accompanied by cuts in white-collar staff and in service-related jobs.
Further changes now in the works at GM are also likely to fall hardest on the Midwest (see figure 4). The company plans to cut 75,000 more jobs; over two-thirds will be in the Midwest, approximately half in Michigan. Assuming a multiplier effect of two this will cost the Midwest 100,000 more jobs downstream. Additionally, GM has indicated it may eventually cut 30,000 white-collar jobs—10,000 above current forecasts. Most will be in Michigan, home of GM’s divisional activities and world headquarters.
4. Big Three assembly plant closings since 1979
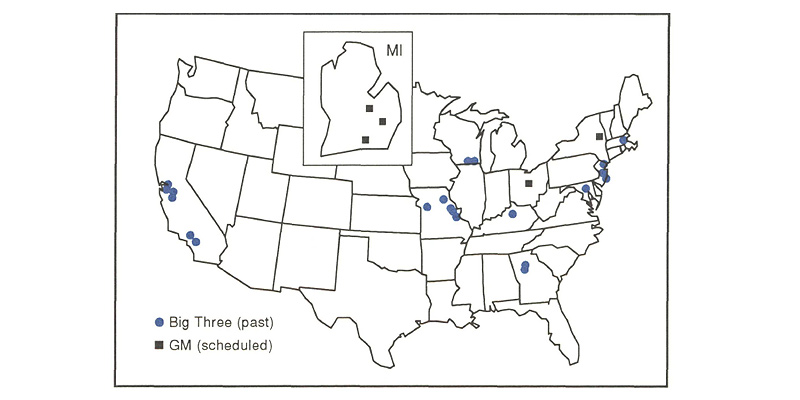
At the same time, the location of foreign transplants in the Midwest has spurred domestic productivity and boosted the region’s suppliers. These transplants are comparable to the best-run U.S. facilities and are increasingly competitive, even with Japanese domestic facilities. Additionally, while transplants originally tended to rely on foreign-made parts, they are now beginning to use parts made by domestic companies or by other transplants. This shift may substantially boost Midwest economic activity, especially if transplants increasingly displace imports and not U.S. brands. In fact, that has been the scenario for the past few years, as U.S. brands have maintained their market share, transplant production has grown, and imports have fallen.
Looking to the future
Given these trends, the Midwest’s future looks brighter than its recent past. Gains by the auto industry, combined with some diversification in the region, spell new opportunities for the Midwest. Nonetheless, a variety of conceivable events, from industry changes to a destabilizing policy environment, could exacerbate the problems of the Big Three and the Midwest.
Whatever the future brings, the region clearly must address a number of issues. First, even after GM closes facilities and reduces the payroll, its present difficulties may not be over. The company faces an increasingly competitive environment, yet it remains burdened with dated products. According to industry analysts, GM must upgrade its product mix and improve its quality and base technology—tasks requiring substantial research and development. If GM continues losing market share, it will have to downsize even further, and the Midwest would feel these cuts most strongly.
Second, the industry’s current market environment is extremely volatile. Cyclical factors, specifically the weak markets in the developed world, have prompted cost-cutting by most major manufacturers. More importantly, structural changes are leading to shifts in the location of manufacturing activity and in the activity itself. Increasing responsibility for production is being placed on suppliers, with the Big Three and foreign companies focusing more on design, assembly, and marketing. The full impact of these changes has yet to be fully realized.
Third, as noted previously, the long-term prospect for vehicle sales in the U.S. is uncertain. Although not everyone agrees on the magnitude of the problem, most analysts agree that sales will grow only moderately at best. By contrast, markets in the developing world are growing rapidly and promise to heat up still more in the future. Both domestic and foreign automakers face these contradictory trends as they try to plan for the future. Of course, if export growth accelerates, the net impact of these trends may be positive for both the industry and the Midwest.
Finally, as the Midwest loosens its dependence on autos yet struggles to keep the industry in the region, government development policies can significantly affect both industry and region. The U.S. economic environment today is far different from previous decades. Resources are more mobile, markets are more competitive, and in terms of growth, the U.S. domestic market is slowing relative to other markets. Accordingly, government policies should seek to make the region and the nation competitive for business location and growth.
What, then, does the future hold for the auto industry and the Midwest? There are more questions than answers. Many of the questions reflect major, potentially ominous, concerns. Yet offsetting trends may help soften the shocks of GM’s current troubles. Overall, the auto industry and other core Midwest industries are in better shape to compete in the world market than they were just a decade ago. In turn, the Midwest is now one of the healthiest regions in the nation.
Nevertheless, one prediction is clear: The auto industry will continue making difficult transitions, and the Midwest will feel the effects. Learning from the past, the industry and the region should be able to meet these challenges wisely and well.
Tracking Midwest manufacturing activity
Manufacturing output index (1987=100)
March | Month ago | Year ago | |
---|---|---|---|
MMI | 118.4 | 118.0 | 110.4 |
IP | 113.4 | 113.3 | 108.5 |
Motor vehicle production (millions, saar)
March | Month ago | Year ago | |
---|---|---|---|
Autos | 6.2 | 6.3 | 5.2 |
Light trucks | 4.8 | 4.3 | 3.8 |
Purchasing Managers’ Surveys: production index
April | Month ago | Year ago | |
---|---|---|---|
MW | 61.5 | 66.3 | 58.6 |
U.S. | 51.8 | 57.4 | 56.9 |
Motor vehicle production, millions (saar)
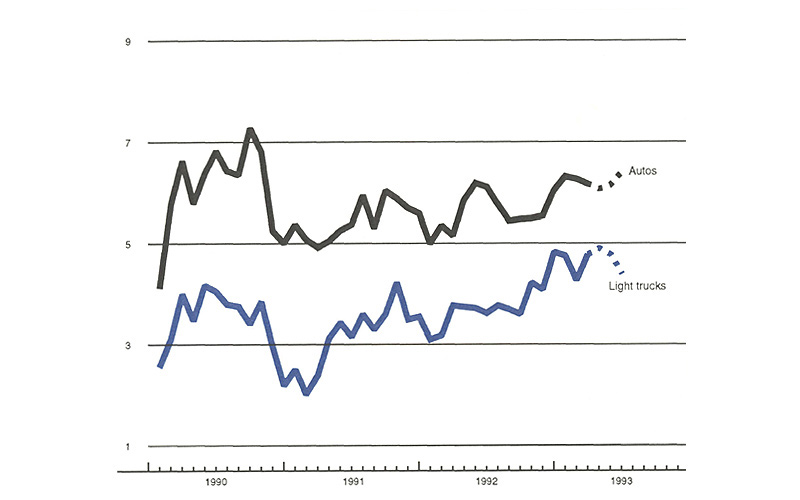
Note: Dotted lines are estimated production.
Sources: The Midwest Manufacturing Index (MMI) is a composite index of 15 industries based on monthly
hours worked and kilowatt hours. IP represents the FRBB industrial production index for the U.S.
manufacturing sector. Autos and light trucks are measured in annualized physical units, using seasonal
adjustments developed by the Federal Reserve Board. The PMA survey for the U.S. is the production
components of the NPMA survey and for the Midwest is a weighted average of the production components of
the Chicago, Detroit, and Milwaukee PMA survey, with assistance from Bishop Associates and Comerica.
Midwest manufacturing has grown modestly in recent months, boosted by a rise in car and light truck production since mid-1992. But total production in April was unchanged from March. A slight gain in light truck production offset a slight drop in car production.
Planned car and light truck production for the rest of the second quarter should help keep Midwest expansion on track. Light truck production will be almost flat in May and June, partly because of early model changeovers. But car production should increase by 100,000 units in May and 200,000 units in June. If sustained, the June car production rate (annualized at 6.4 million units) will be the highest since late 1990.
Notes
1 Among the most comprehensive studies of the auto industry are The Machine that Changed the World, by J.P. Womack, D.T. Jones, and D. Roos (Macmillan Publishing Company, 1990); Rude Awakening: The Rise, Fall, and Struggle for Recovery of General Motors, by M. Keller (Morrow, 1989); and The Harbour Report a Decade Later: Competitive Assessment of the North American Automotive Industry, 1979-1989 (Harbour & Associates, Inc., 1990).
2 This number includes fleet sales, which are dominated by the Big Three. Erosion at the retail level (which excludes fleet sales) is even more severe, with market share of domestic brands declining to under 60%.
3 Japanese automakers have traditionally used a four-year cycle as a standard. Recent design and development innovations have aimed to cut this down to three years. Chrysler has tried to match this ambitious schedule with its L-H and PL models.
4 The Motor Vehicle Manufacturers Association estimates that approximately 3 million jobs in the Midwest are motor vehicle related. This number does not include jobs in the service sector that are affected by events in the auto industry. Studies on the impact of plant closings find a very strong link between the auto industry and area service activities.