New car buyers face limited inventory, long order wait times, and rising prices primarily because of lingering automotive supply chain disruptions. It is difficult for automakers to produce enough vehicles to meet demand, and the main culprit is reported to be the lack of semiconductors—or chips. Professional forecasters have ratcheted down their sales and production predictions as the months go by, and the supply-constrained conditions have not returned to pre-pandemic levels. In this article, I investigate why the chip crisis is still with us and why some forecasts suggest that it will continue at least into 2024.
Specifically, in this Chicago Fed Letter, I look at the origins of the chip crisis, factors driving increased chip content in vehicles, the market dynamics for different types of chips, semiconductor industry investments, the role of public policy and automotive firm strategies in addressing the crisis, and the factors that could improve or worsen future automotive semiconductor supply.
A combination of factors led to the chip crisis
The oft-mentioned chip crisis is only one part of the automotive supply challenges the industry is facing. The pandemic snarled global supply chains and logistics for many other raw materials and manufacturing inputs, and manufacturers are finding it challenging to fully staff their operations in this tight labor market. Yet the chip shortage is what still garners headlines.1 The common narrative is that the auto industry sharply pulled back its semiconductor orders as the pandemic shock took hold in early 2020—which is also when other industrial sectors such as those producing consumer electronics increased their chip orders to meet rising demand for equipment that facilitated work-from-home arrangements and remote schooling. Chip manufacturers allocated capacity to serve these sectors with growing needs, and it is taking some time to reallocate capacity back to serving automotive demand. While the narrative is accurate, it is incomplete. The semiconductor supply issues run much deeper and wider, and the imbalance in semiconductor supply and demand for the auto industry is lingering far longer than many industry observers initially expected. The solution is not solely about reallocating capacity.
Auto manufacturers throughout the world continue to struggle to produce light vehicles at pre-pandemic rates. Figure 1 shows monthly U.S. light vehicle production from January 2019 through August 2022. As a result of the pandemic, auto production fell to lower levels in March through June of 2020, but output quickly rebounded to 2019 “normal” levels in July through October of that year. Then, starting in November 2020, supply chain issues started to surface, and output dropped again below 2019 levels and largely stayed there through July 2022. August 2022 was the first month since December 2020 when U.S. light vehicle production returned to 2019 levels. On an annualized basis, U.S. light vehicle production averaged 11.2 million units in the five years before the pandemic and hovered just below 9 million units in 2020 and 2021; output is now forecasted to end 2022 with just under 10 million units produced. Underproduction is not only a U.S. problem; global supply chain disruptions have led to over 35 million fewer vehicles projected to be produced worldwide in 2020, 2021, and 2022 than would have been built had automakers continued manufacturing vehicles at 2019 output levels.2
1. U.S. monthly light vehicle production, January 2019–August 2022
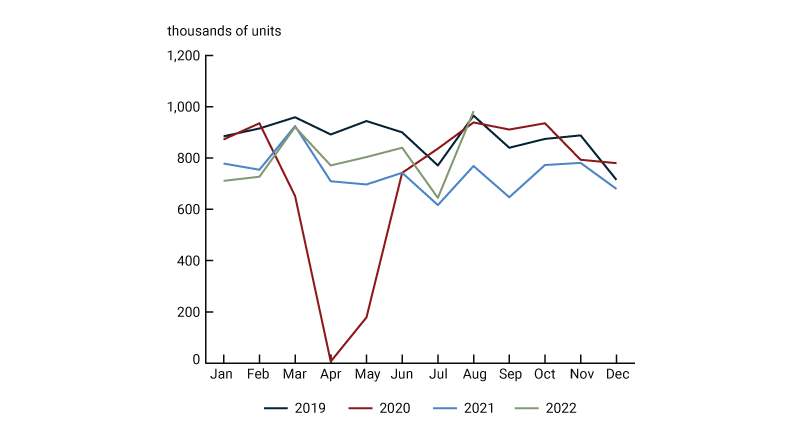
In addition to a sharp shift in automotive chip order volumes, the semiconductor industry has also been affected by unseasonably cold weather in Texas in early 2021, a lingering drought in Taiwan, an earthquake in Japan followed by a fire at a key automotive chip supplier, and Covid-19-related shutdowns in China and other chip-manufacturing countries. Russia’s invasion of Ukraine also had an impact, as Ukraine was the world’s largest producer of highly refined neon gas and Russia is a major producer of platinum group metals; both resources are used in semiconductor manufacturing. The combination of these factors continues to make it more difficult to supply sufficient output to meet global semiconductor demand. S&P Global estimates that semiconductor lead times have stretched to as much as four times as long as they were before the pandemic—which means the chips arriving in factories in 2022 were likely ordered sometime in 2021.3 While automakers report that semiconductor supply is starting to normalize—meaning the chips they ordered show up when they expect them—the imbalance in supply and demand may persist well into 2023—and likely beyond.
Technological advancement drives greater chip demand
An individual light vehicle may have hundreds of different semiconductors in it, but the growth of new vehicle technologies—such as vehicle electrification, advanced driver assistance systems (ADAS), connectivity (plus cybersecurity), and additional vehicle automation—means that each new vehicle has increasingly more chip content. Because of the demand for vehicles with these advanced features, even sustained 2019 levels of semiconductor supply would be inadequate to produce the same number of vehicles today. The average number of chips per vehicle doubled between 2017 and 2021 and is continuing to grow (S&P Global Mobility, 2022). Chip content growth—both in number and dollar value—is poised to accelerate even further as more vehicles come equipped with increased safety features, automated driving capability, and hybrid or battery electric propulsion systems. The market research and advisory firm Gartner forecasts that the total value of the global automotive chip market will grow from $38.7 billion in 2020 to $116.6 billion by 2030 (at a compound annual growth rate of 11.7%).4
Semiconductors not only enable greater electrification, automation, ADAS, and safety applications, but also are critical to vehicle instrument clusters, infotainment systems, body and chassis applications, and internal combustion engine and transmission controls. Vehicles are producing more data than ever before, and the growing need for memory, data storage, processing, and connectivity to cloud-based storage is driving up automotive chip demand. Increasingly, automakers are moving to new vehicle architectures such as the software-defined vehicle that include high-performance computing—an area that Gartner expects to grow from $0 in 2020 to $13.8 billion by 2030 (Yamaji, 2022). So, while the absolute number of chips per vehicle may eventually decrease in the future when software-defined vehicles become dominant, the overall value of the chips per vehicle is expected to increase through the end of the decade.
Different types of chips are subject to different competitive forces
Automotive semiconductors come in many varieties, and vehicles need many different types of chips to perform specific functions. There are three main categories of semiconductors:
- analog chips—which are used to perform an action on a physical system (e.g., a switch used to move a windshield wiper motor);
- microprocessors (MPUs) and microcontrollers (MCUs)—which process data and control systems (such as engine controls or tire pressure monitoring); and
- other chips—which include memory, sensor, digital signal processor (DSP), and optoelectronic chips.
Semiconductors are used in a wide range of applications in the vehicle—from a simple memory system that recalls your preferred seat position to complex battery management systems that manage charging, battery life, and thermal variation. It makes sense, then, that the industry relies on a wide array of semiconductor types for different uses.
What’s more, “automotive grade” sets a high bar for semiconductor performance, reliability, and durability. You wouldn’t leave your smartphone or computer in your driveway in rain, snow, or dangerous summer heat. But the electronics in your vehicle must withstand not only extreme hot and cold temperatures (–40°C to +150°C, according to the Automotive Electronics Council, 2014), weather events, and moisture, but also vibration, dirt, and chemicals (especially petrochemicals) in the environment. In addition, the average vehicle currently in operation is more than 12 years old. In other words, automotive-grade semiconductors must be more rugged, reliable, durable, and robust than chips used in most consumer electronics, home appliances, or other devices generally used indoors; in addition, given the critical safety nature of transportation, automotive-grade semiconductors must also be more protected from electronic interference and cybersecurity threats than most other chips. As such, the automotive industry tends to use “mature” or “legacy” semiconductor technologies, which are more proven. Roland Berger estimates that of the more than 1,000 semiconductors in an average internal combustion engine vehicle, 95% are considered mature or legacy chips compared with about half of the chip content in an advanced battery electric vehicle. The chip content in a battery electric vehicle more closely resembles that of a high-end laptop or medical MRI (magnetic resonance imaging) scanner than that of an internal combustion engine vehicle.5 The capacity to produce mature and legacy semiconductors that modern automobiles rely on is not growing as fast as the production capacity of the overall chip industry; analysts say mature and legacy chip capacity is expanding at 2% per year versus over 10% annual growth for semiconductor capacity overall.6
The automotive industry is also characterized by relatively long development cycles (especially relative to product development in the semiconductor industry), rigorous supplier qualification processes, long production runs (seven to nine years),7 and a need for ten-plus years of aftersales support.8 In the fast-moving semiconductor industry, these timelines equate to multiple generations of semiconductor products. A semiconductor manufacturer may be able to supply a more capable or lower-cost component during the auto industry’s long product timeline; but to ensure components do not fail causing accidents or deaths, the auto industry’s strict quality standards, testing, and qualification processes must be followed.
The automotive industry accounted for roughly 8.6% of the global market for semiconductors in 2021; by 2030, Gartner estimates that share could grow to over 12.5% of global semiconductor output (Yamaji, 2022). For some chip segments, the automotive sector is a small player with little market power, but for others—most notably analog chips—automotive is the largest end market and consumes most of these segments’ global output (S&P Global Mobility, 2022). This position of market dominance has historically allowed the auto industry to dictate the terms to chip suppliers. But with increasing demand for chips, the high investment costs of increasing chip capacity, and the low returns for chipmakers that sell mature or legacy technology chips (which, while specialized, are mainly low-cost products), automakers need new strategies to secure future chip supply.
The U.S. public policy response to semiconductor supply disruptions
With automotive output crippled by semiconductor supply constraints and the U.S. defense suppliers also highly reliant on the same supply chains, it is not surprising that the federal government would intervene to try to resolve the underlying issues. U.S. policymakers have long considered semiconductor supply a critical issue for national security—even before the pandemic took hold and chip supply began to constrain automotive output. The U.S. share of global semiconductor manufacturing capacity dropped from 37% in 1990 to 12% in 2020.
Back in the mid-1980s, the U.S. and Japan signed the Semiconductor Trade Agreement to address trade imbalances and resolve an anti-dumping dispute with Japan (Baldwin, 1994; and Bown, 2021a). Between 2017 and 2020, the Trump administration pursued a wide range of trade actions, including tariffs and export controls, primarily against China, aimed at protecting U.S. national security in high-technology industries—including the semiconductor sector. As the largest consumer of both semiconductors and semiconductor equipment and the sixth-largest source for the U.S. for semiconductor devices and electronic integrated circuits and microassemblies,9 China is both a critical—and growing—part of the global semiconductor industry and a main target of recent U.S. semiconductor export controls under both the Biden administration and the Trump administration.
When President Biden took office, one of his first executive orders was to commission 100-day reviews under Executive Order 14017 that included an investigation into U.S. semiconductor supply (White House, 2021). The 100-day reviews of supply chains proposed a range of public and private sector strategies to build a more “secure and resilient semiconductor supply chain” (White House, 2021, p. 74). These included promoting investment, fostering innovation, training the semiconductor workforce, and forging international partnerships to “friend shore” semiconductor supply, with chips coming from manufacturers located in countries and regions that are longtime U.S. allies, such as Japan, South Korea, and the European Union (White House, 2021; and Bown, 2021b).
The 100-day reviews also explicitly supported the then-pending bipartisan Creating Helpful Incentives to Produce Semiconductors (CHIPS) for America Act of 2022.10 In August 2022, President Biden signed the CHIPS Act that provides $52 billion to incentivize U.S. semiconductor manufacturing. While the CHIPS Act provides “carrots” to invest in U.S. chip-making capacity, the Biden administration has also stepped up its use of “sticks” in the form of increased enforcement actions and export controls to protect semiconductor technology the U.S. deems essential to U.S. national security. In June 2022, the U.S. Bureau of Industry and Security (BIS) announced stricter enforcement of export controls to protect sensitive technologies, and in August 2022, BIS banned the export of four technologies that the U.S. determined are essential to U.S. national security. Additional export controls were enacted in October 2022, resulting in swift changes in the Chinese semiconductor industry as companies work to come into compliance with the new regulations.
The supply chain report’s recommendations and the CHIPS Act funding address many of the issues that constrain U.S. automakers’ chip supplies, but none of these policies provide quick or complete fixes to the immediate supply crunch. Investments in new chip production capacity can take as long as three to five years to come on line, and companies that invest in U.S. production sites are more likely to do so for higher-revenue, cutting-edge technologies that will only address part of the problem for U.S. automakers. The CHIPS Act’s $52 billion is a substantial sum, and the auto industry welcomed the $2 billion set aside for mature technology capacity expansion. However, the size of semiconductor fabrication investment is so large that this funding may not be sufficient to tip the scales in favor of large-scale U.S. chip production.
The auto industry’s response to semiconductor supply disruptions
The auto industry is not waiting for government solutions to the semiconductor crisis. Automakers and suppliers are pursuing multiple strategies to better position their firms given the industry’s greater reliance on semiconductor content for future vehicle technology.
The pandemic market disruptions and increasing technology content on vehicles suddenly made semiconductors—which were once thought of as just a commodity—a very strategic input on par with battery raw materials. This shift left automakers and suppliers scrambling to rebuild buffer stocks, tie up dedicated capacity through partnerships and joint ventures, and rethink their strategies around the numbers and types of different chips that they use in their vehicles.
The first strategy is to streamline and rationalize the number of different types of chips to a smaller number of variants. This strategy enables greater purchasing power with the providers of those semiconductors; fosters partnerships between automakers, suppliers, and semiconductor producers; and even facilitates co-investment arrangements that will secure the industry’s future chip supplies. Co-investment and partnering strategies will also improve the auto industry’s visibility into semiconductor supply chains—which could lead to improved vehicle production volume planning.
Second, automakers and suppliers are designing flexibility into the semiconductor supply by qualifying multiple supply sources, according to several industry contacts. The supplier qualification process is costly, can take months, and must be completed not only for each product and firm but for each manufacturing site. By qualifying more sources up front, auto industry producers can more easily switch between available suppliers should one firm or one country face challenges such as natural disasters or geopolitical instability.
Ultimately, automakers are moving toward greater integration of vehicle software and hardware in the software-defined vehicle mentioned earlier. The emergence of these more flexible architectures means replacing multiple semiconductors with more high-performance computing modules. While this strategy changes the types of semiconductors used, it may not decrease the total semiconductor value per vehicle. Automotive is a much smaller share of the market for advanced semiconductors needed for high-performance computing, and so the auto sector will face continued price and allocation pressures due to chip demand from other industries. However, automakers and parts suppliers may realize efficiencies in using fewer wire harnesses and less copper content in the software-defined vehicle. While some automakers are already selling these types of vehicles in the market today, it will take a decade or more for this approach to vehicle architecture to become dominant in the U.S. market.11
Outlook
When will the automotive semiconductor shortage end? Unfortunately, it is difficult to say as both supply and demand dynamics continue to shift, and the array of public policy and industry responses will take time to play out. Overall, semiconductor supply disruptions are starting to ease as production and demand come more into balance and orders arrive at the factories on a more regular basis, though lead times continue to grow longer. Most industry forecasters see a return to a “more normal” semiconductor supply in late 2024. However, semiconductor supply chains are long and are exposed to many types of disruptions, including the continuing unpredictability of the Covid-19 virus and responses to it.
The global semiconductor industry is in a period of rapid expansion. Companies are investing in locations throughout the world, and several large international firms have recently announced plans to build semiconductor manufacturing capacity in the United States. For example, Taiwan’s TSMC is building a $12 billion manufacturing facility—Fab 21—just outside Phoenix, Arizona, with plans to build up to six factories on the site. U.S. chip manufacturer Intel also recently announced a $20 billion investment near Columbus, Ohio. Many other companies are considering U.S. locations for expanded chip manufacturing capacity investments.
The one thing these investments have in common is that they are all for cutting-edge advanced semiconductor production. The automotive industry relies on some chips produced using these advanced design architectures and processes; however, as explained earlier, many more automotive chips are made using mature or legacy designs and processes. In a business where new chip fabrication plants can cost upward of $10 billion, relatively more investment is going toward expanding capacity for advanced process chips rather than mature or legacy technologies as it is more difficult to amortize the upfront investment for lower-cost semiconductor products. The semiconductor industry’s rational investment priorities mean that the automotive industry may need to move to more advanced—and more costly—chip content faster than it otherwise would have or co-invest in expanding manufacturing capacity for mature or legacy technology chips. For some applications, only the mature or legacy technology chips will do.
Here are a few of the other trends that could impact the future automotive semiconductor market and automotive supply conditions more broadly:
- Disruptions beyond chips. While 2021’s lost global production was mainly about semiconductor shortages, 2022 shortages involve a wider array of parts and components. With a range of natural and man-made disasters, it seems there is always something snarling the auto industry’s complex global supply chains. In such chains, managing disruptions was common before the pandemic. Now, these disruptions are more frequent and more persistent; therefore, it has become more challenging for companies to adjust to maintain their production levels.
- Trade tensions. The U.S. tariffs and export restraints, as well as other countries’ trade actions, can disrupt semiconductor production. It is difficult to forecast where the next trade dispute may arise that will impact the ability of the semiconductor industry to produce.
- Geopolitical tensions. Taiwan is a central player in the global semiconductor industry, and geopolitical tensions between China and Taiwan could be problematic for all semiconductor-based products, not just light vehicles. In addition, resource and energy supply disruptions in Europe that are a result of the ongoing Russian invasion of Ukraine may impact automotive parts and components production.
- Continued cross-industry competition. The origins of the crisis date back to a rise in demand from other industries, such as those producing computers and cell phones, that caused chipmakers to reallocate capacity. The ebbs and flows of chip demand throughout the wide range of modern products will continue to impact both the prices and supply of automotive semiconductors.
- Not enough chips to make chips. Even the firms that make semiconductor manufacturing equipment are finding it difficult to source sufficient chip content to fulfill their demand. As capacity expansion and investment ramp up, chip shortages for these critical capital goods producers could hamper the industry’s ability to meet future production demands.
- Uneven investment. Semiconductor investment headlines often tout new wafer fabrication or foundry plants, but as investment ramps up in these high-margin producers, not all parts of the chip supply chain are expanding at the same rate. The lower-margin companies that perform packaging, testing, and other functions may not currently be allocating sufficient capital to head off future downstream production bottlenecks.
- U.S. manufacturing workforce challenges. Manufacturers report challenges in finding sufficient workers to run production, and semiconductor plants are not an exception. Continued tightness in the manufacturing labor market and policies that limit immigration are likely to further challenge the U.S. semiconductor industry’s plans to rapidly expand capacity.
- Booms and busts. The unprecedented level of semiconductor investment and policy attention today could very well overshoot the mark, leading to oversupply conditions and lower prices. While abundant supply and low prices would be good for chip-consuming industries like the auto sector, a slump could constrain chipmakers’ ability to invest and get ahead of the next supply disruption.
Some of my Chicago Fed colleagues and I are closely monitoring automotive semiconductor supply conditions and will continue to update the public on developments in this important sector for the Seventh Federal Reserve District and the nation as a whole.
Notes
1 A Google News search returns over 400,000 news stories on the automotive chip crisis/shortage posted since January 2020.
2 All actual and projected auto production values in this paragraph are from author’s calculations based on data from Wards Intelligence.
3 S&P Global Mobility, 2022, Supply Chain Crisis Update 2—Regional Impact, Automotive Solutions Webinar Series, August 23. Information from this source is cited here with permission from S&P Global.
4 Masatsune Yamaji, 2022, “Forecast analysis: Automotive semiconductors, worldwide, 2020–2030,” Gartner, report, January 5. Information from this source is cited here with permission from Gartner.
5 This information is from consulting firm Roland Berger, cited here with its permission.
6 Wolfe Research, 2022, “IHS cuts 2022 production forecast, silicon could reduce battery costs, rising semi costs,” Wolfe Research Auto Daily, May 17. Information from this source is cited here with permission from Wolfe Research.
7 Author’s calculations based on data from S&P Global, IHS Markit, AutoInsight. These data are used here with permission from S&P Global.
8 The ten years of aftersales support are an industry practice, and a set period of replacement-part availability is not codified in law. What is required under the Magnuson-Moss Warranty Act is that automakers that choose to offer warranties must be able to repair the vehicle, offer a refund, or replace a defective part during the period of such warranties. Further details from the Federal Trade Commission about the act are available online.
9 Data for Harmonized System (HS) Codes 8541 (semiconductor devices) and 8542 (electronic integrated circuits and microassemblies) are from the U.S. International Trade Administration.
10 A section-by-section summary of the CHIPS Act of 2022 is available online.
11 Author’s projection based on current data from S&P Global and Wards Intelligence, as well as on various industry outlook reports, such as Koster, Arora, and Quinn (2021) for Boston Consulting Group (BCG) and Deloitte (2021). Data from S&P Global are used here with its permission.